Take a Look
Below are projects I have worked on over the past few years. Some are university projects, some are from my old workspaces, and some were pure personal interest. Scroll below to see each project sectioned out. I am not big at photos so some projects may be lacking content, I will keep looking for content and update the page once I find it.
The Boat, never finished
Buyonce, or HydroCAT, or Floaty Boaty, or the boat is a project I worked on during my 3rd year of university, for the year long Design, Make and Test project. I was lucky to work with three more talented mechanical engineers on this project.
We made the boat as a remote controlled vessel that can navigate big rivers and collect real time pollution data. That data can then be used for accurate, informed decision making or for efficient pollution model calibration and verification.
I would love to show you a video of the boat running in water, but COVID forced the university to close the workshop two months before the project deadline. We are proud of what we produced and sad we never got to see it live.
Below is a collection of photos found of the construction under progress, renderings of the CAD digital version, and footage of the testing we did for one of the load bearing parts. A video below also show a collision simulation which proves our fibreglass-reinforced hulls can withstand a collision at maximum speed. Another video shows a stress test of one of our parts; we were very surprised to find that the testing apparatus broke before the part itself.
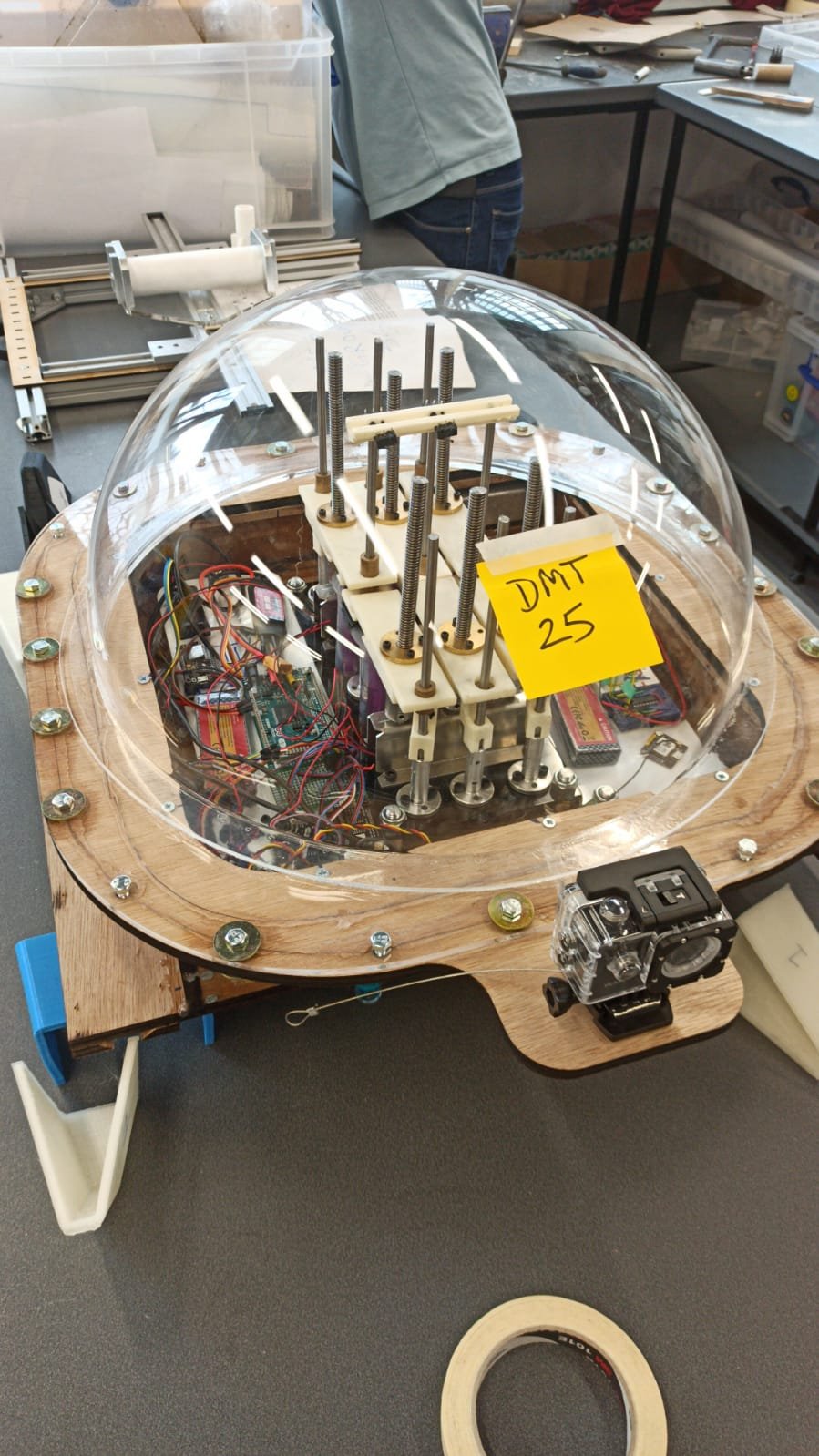
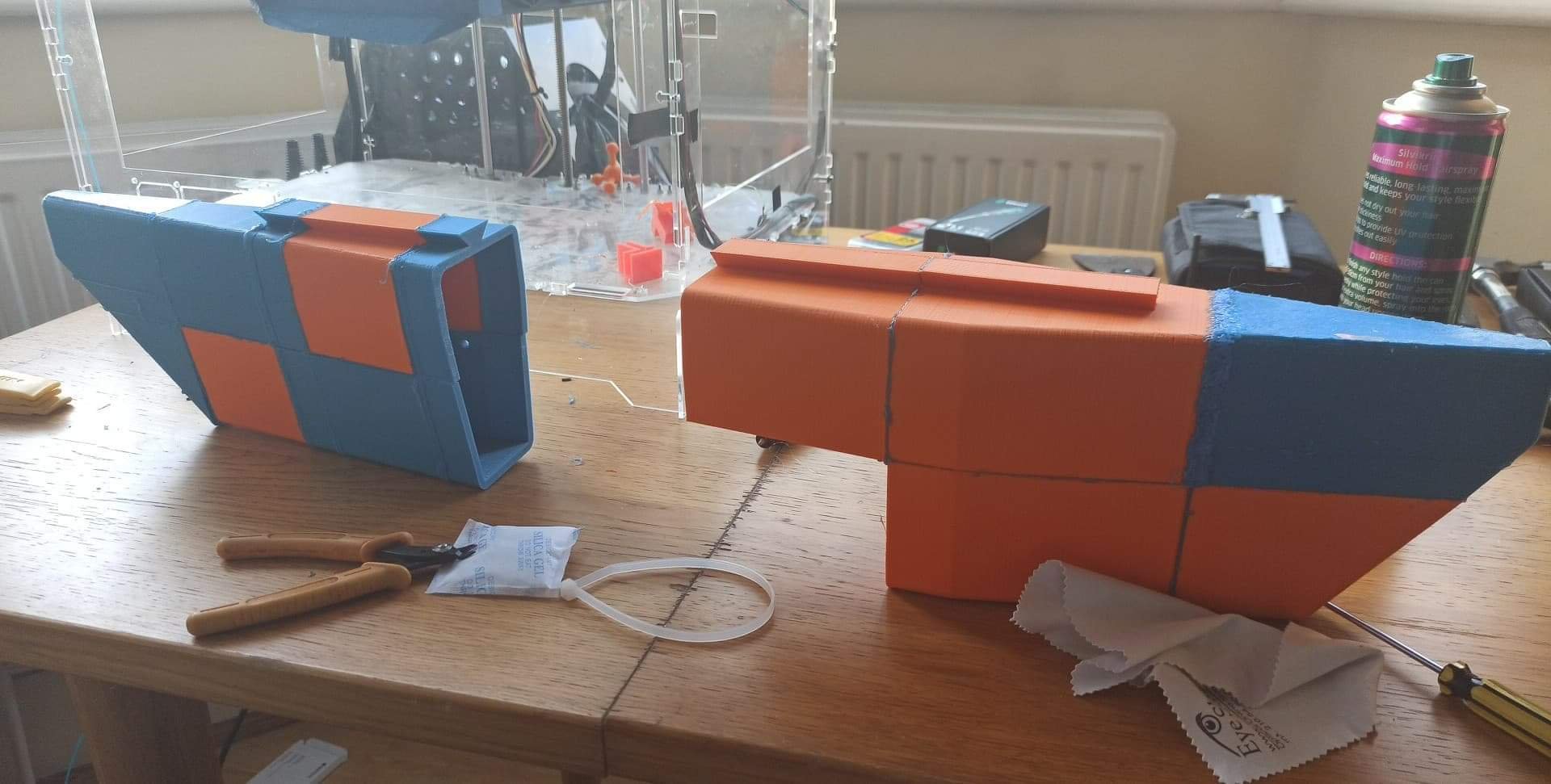
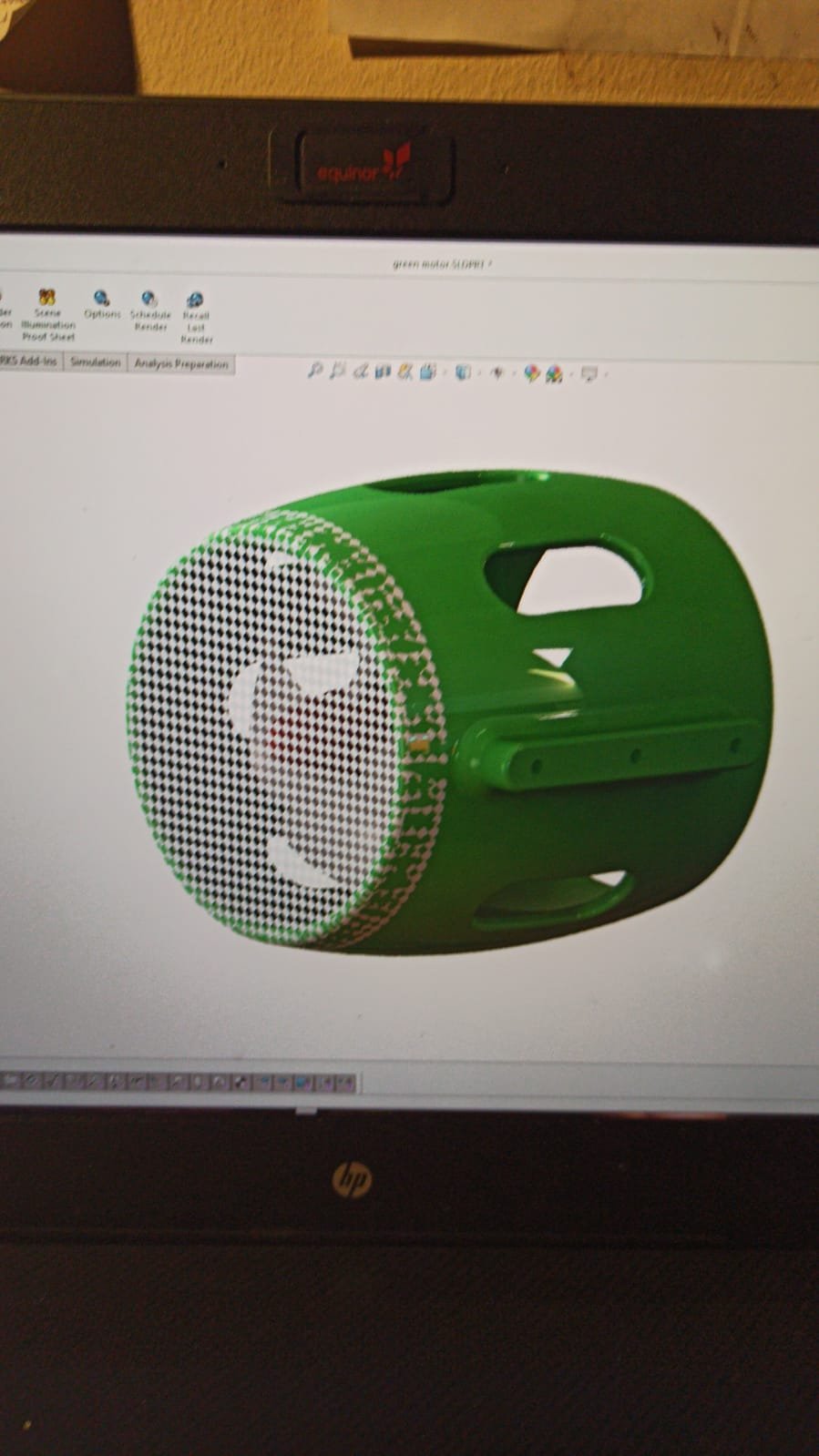
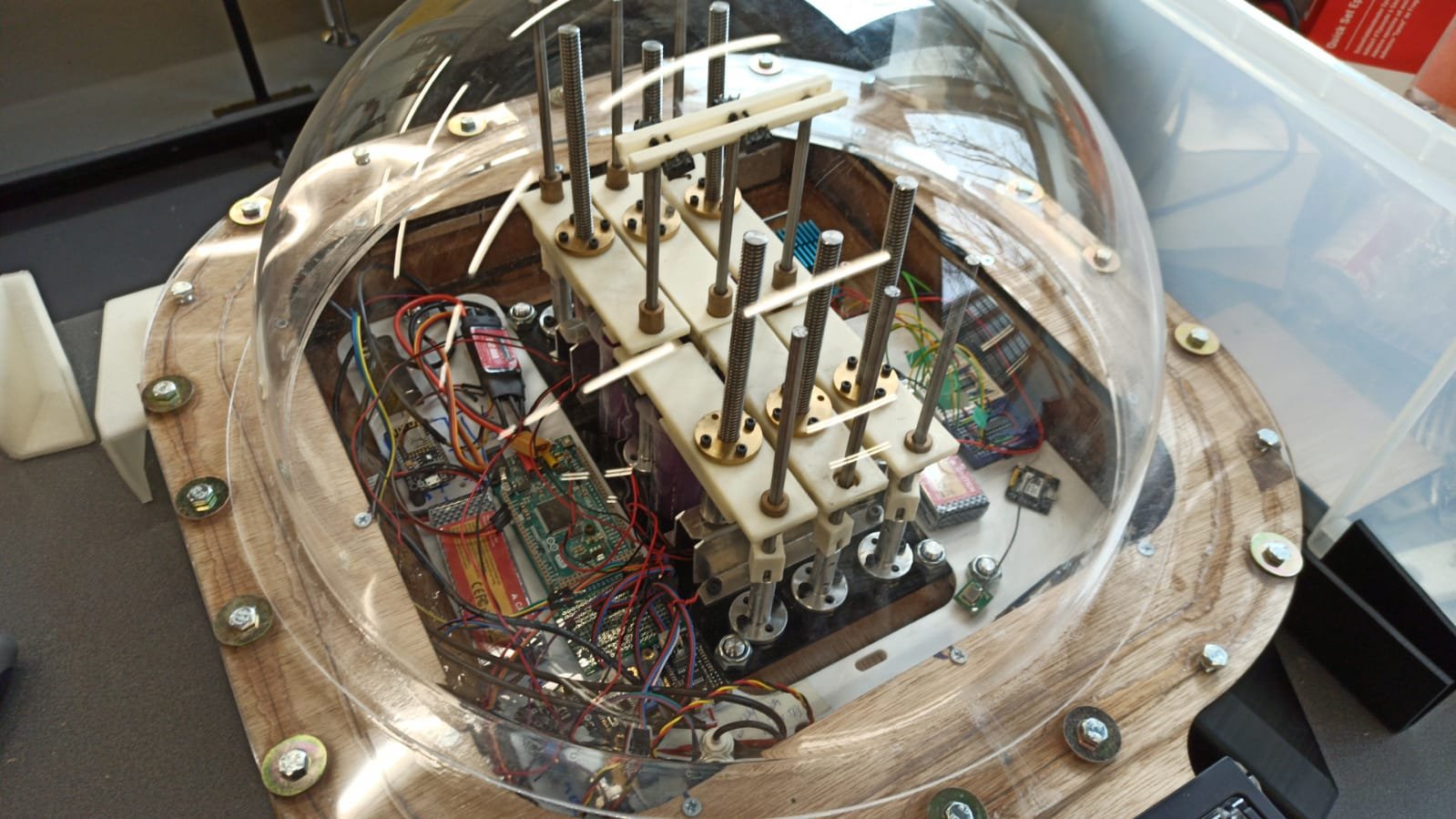

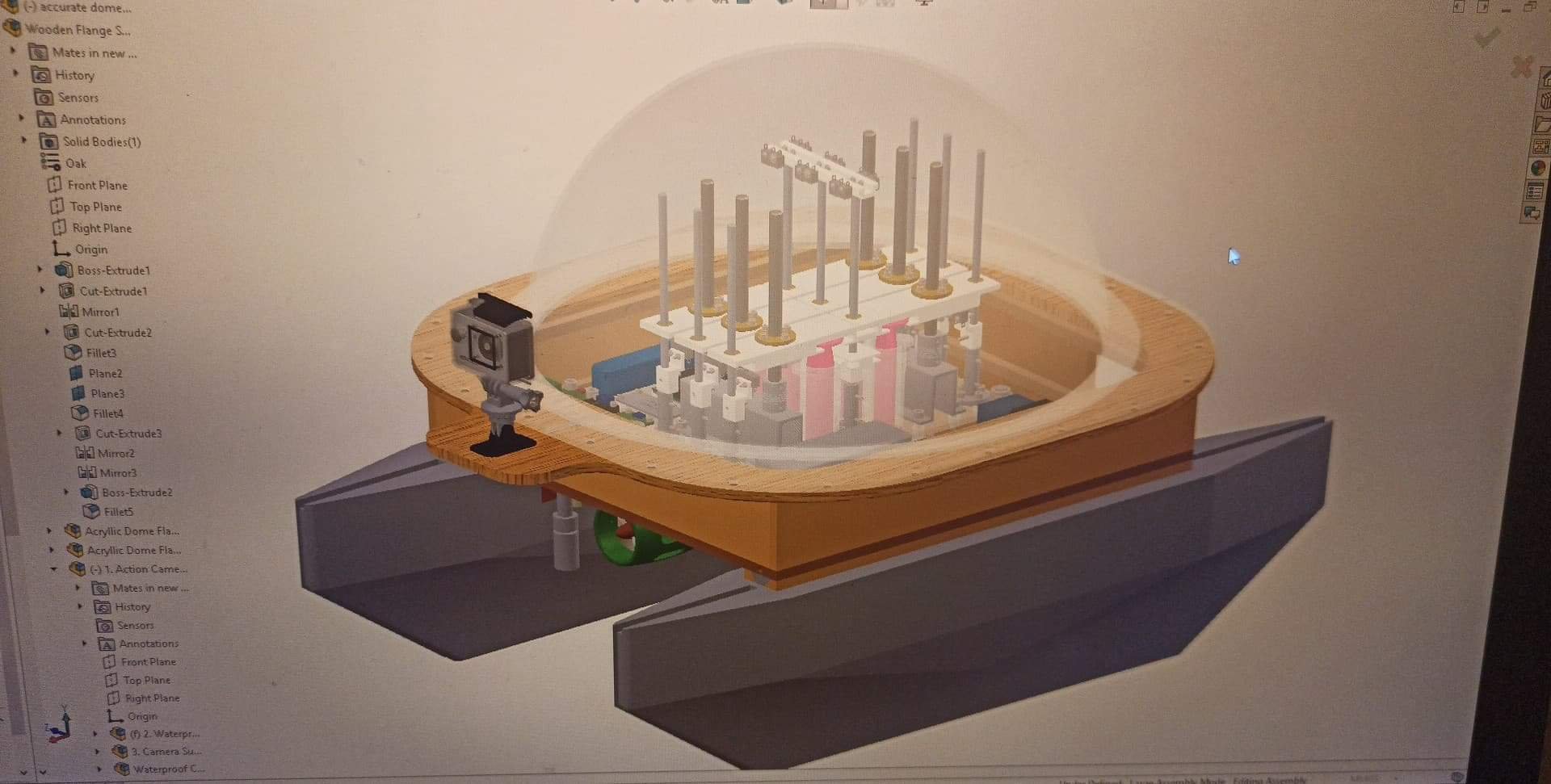
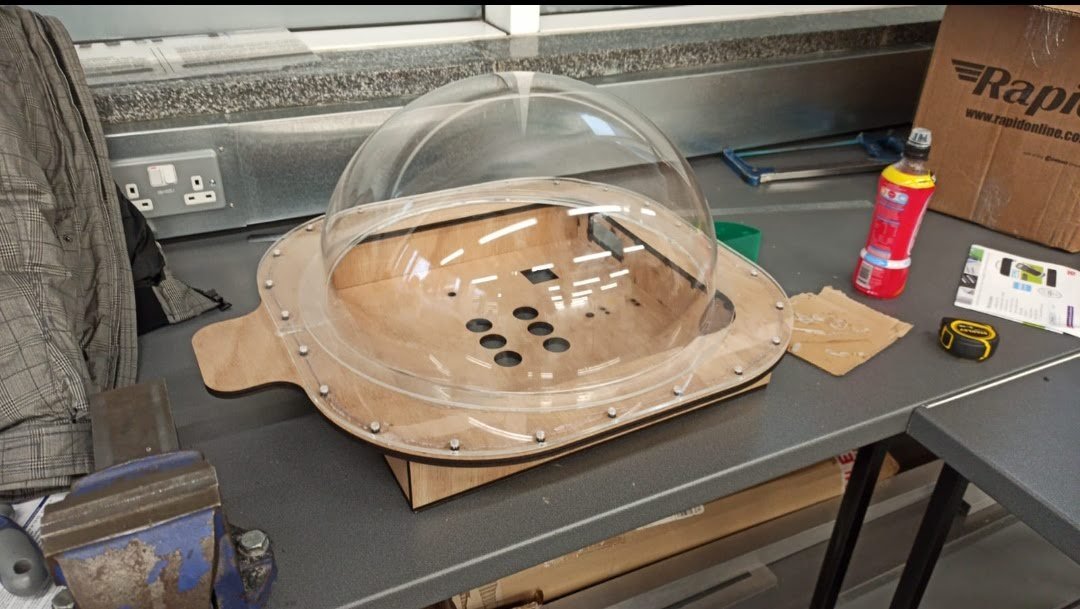
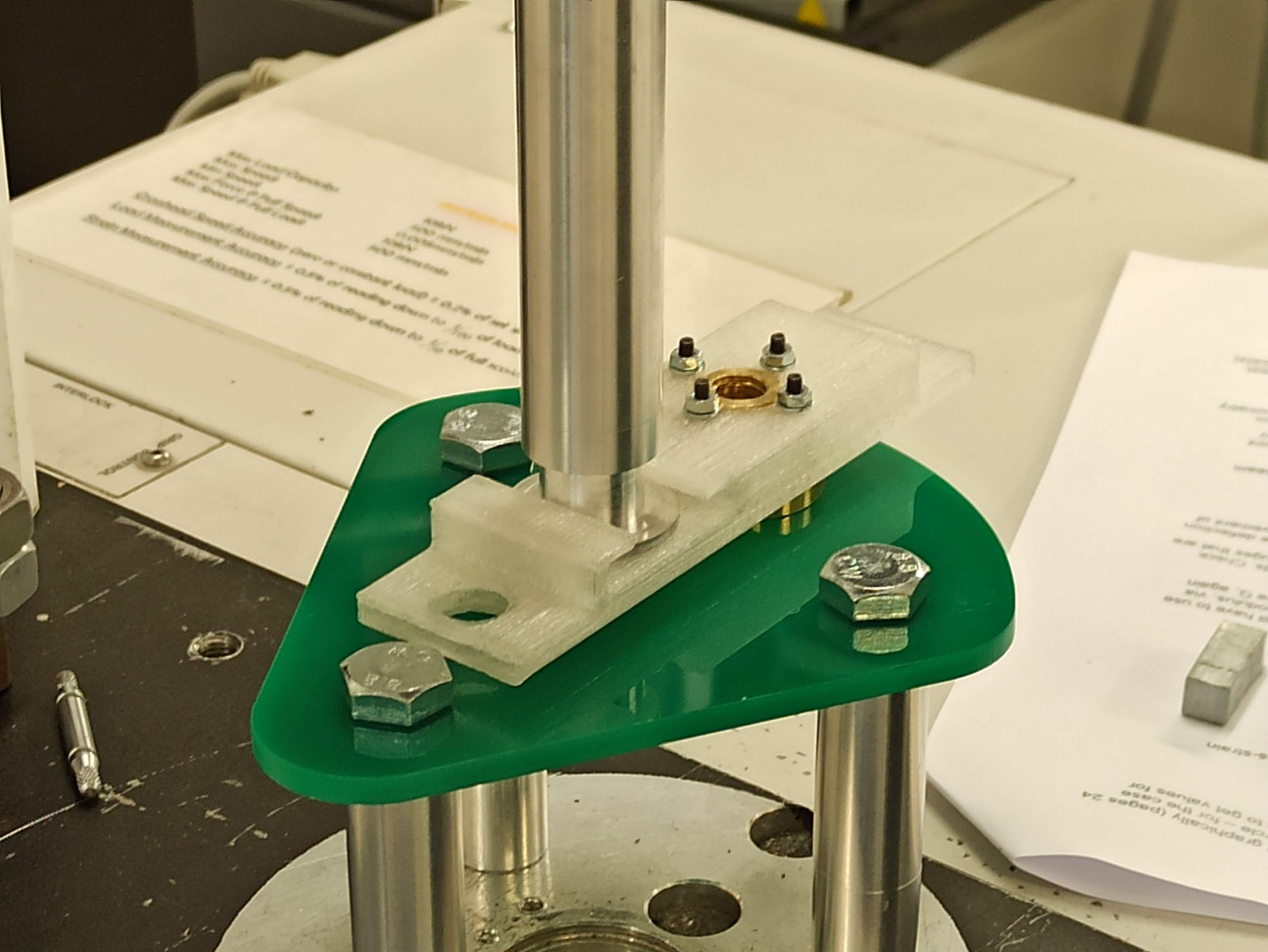
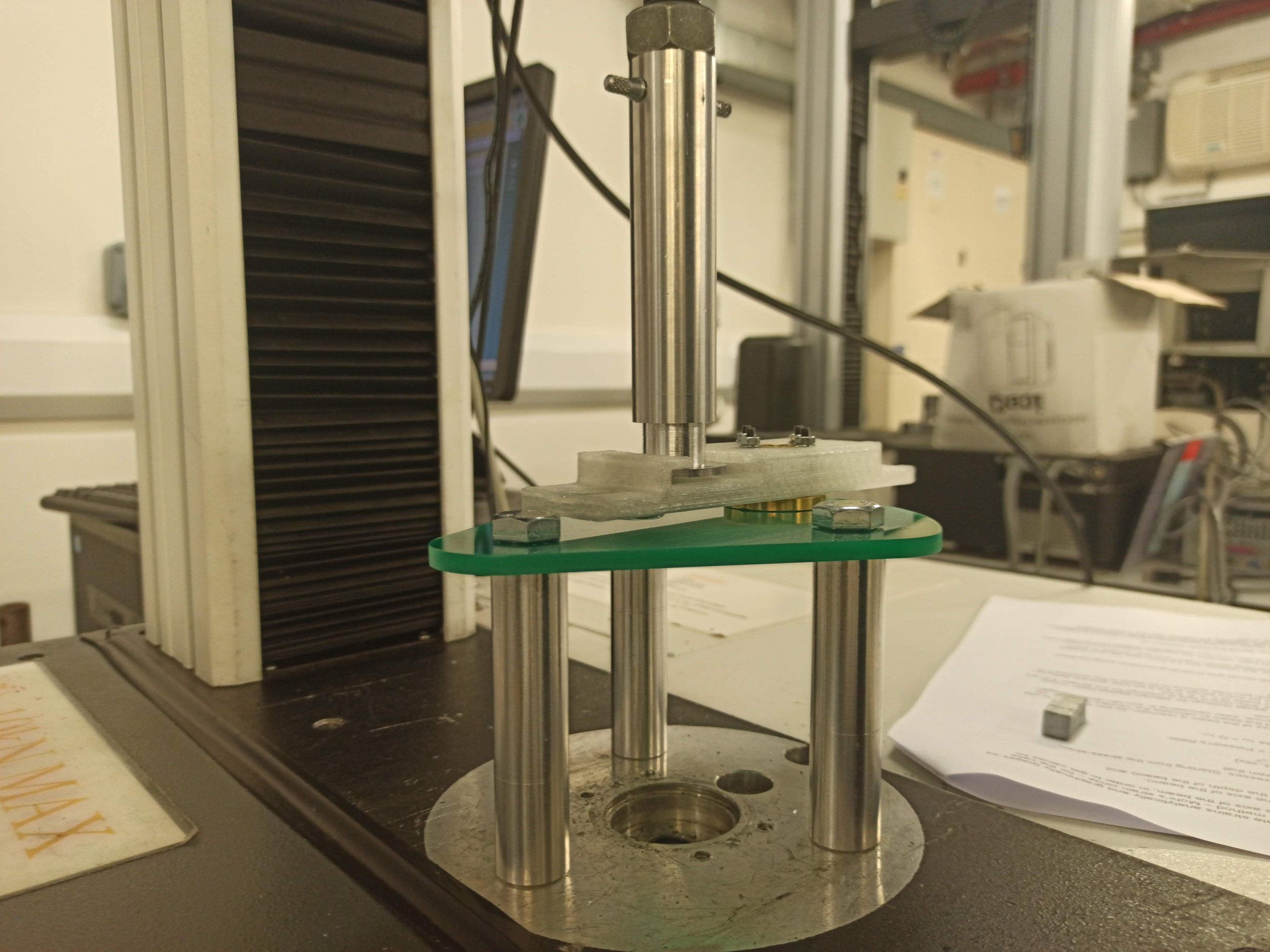
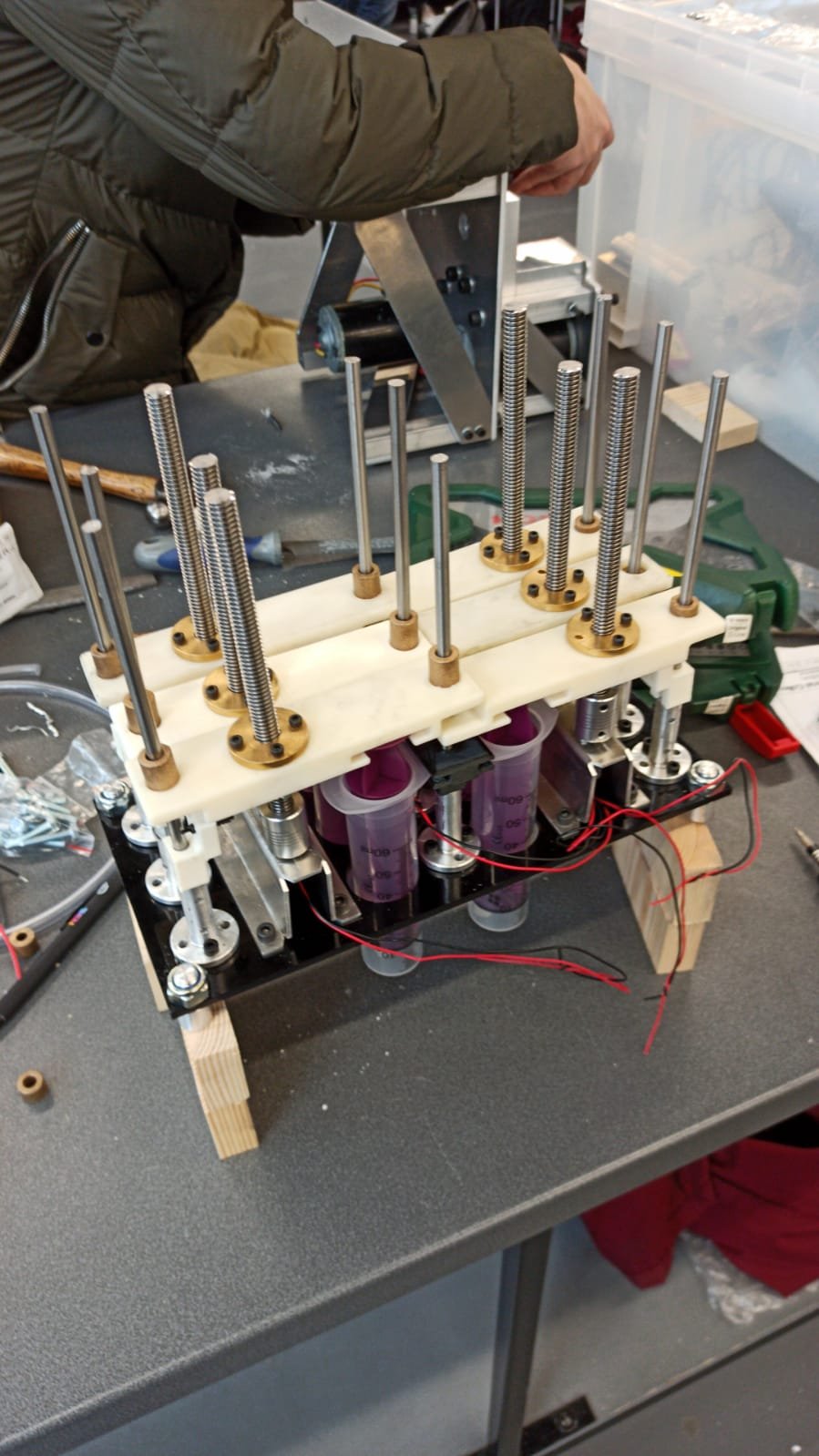
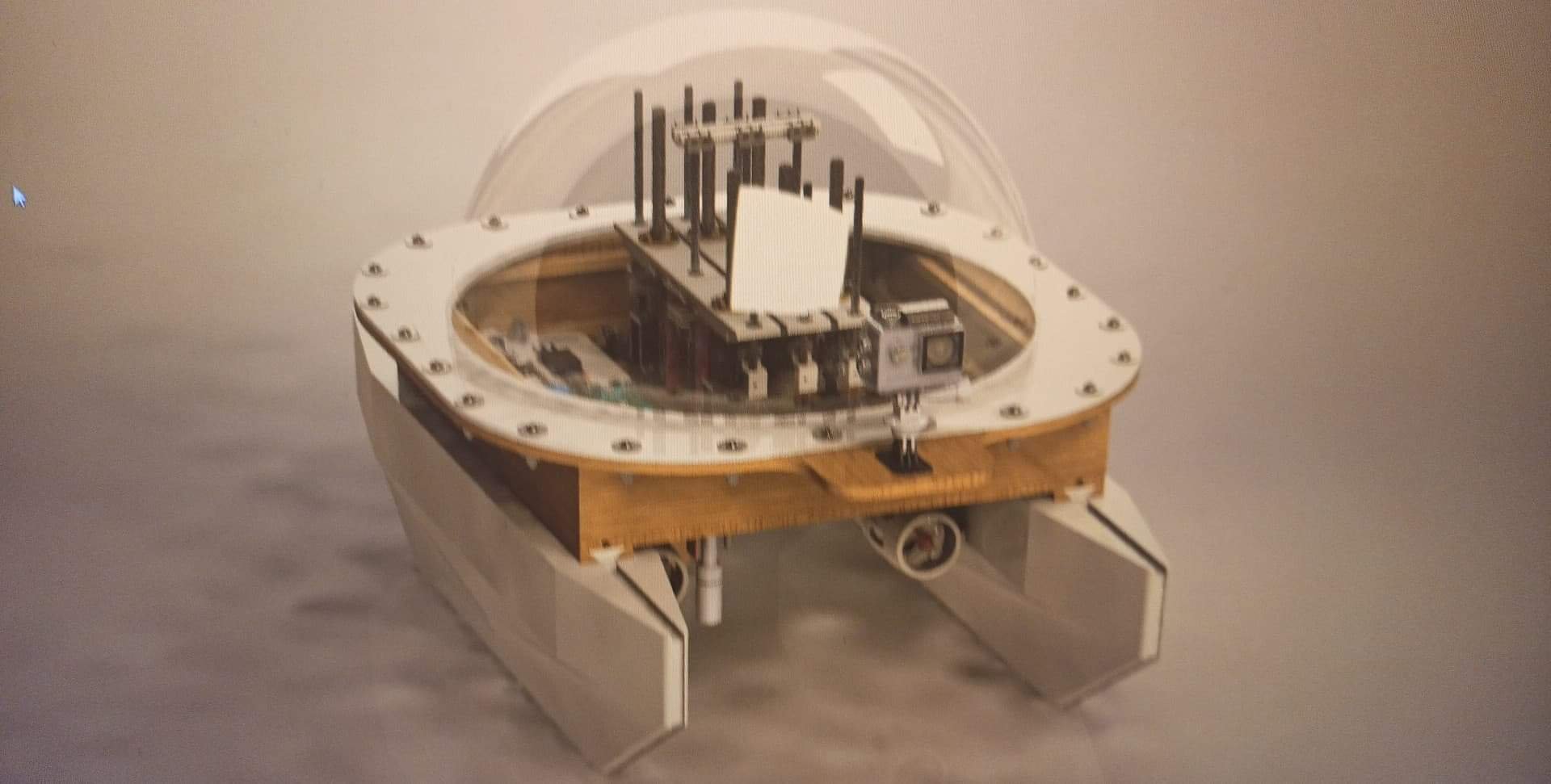

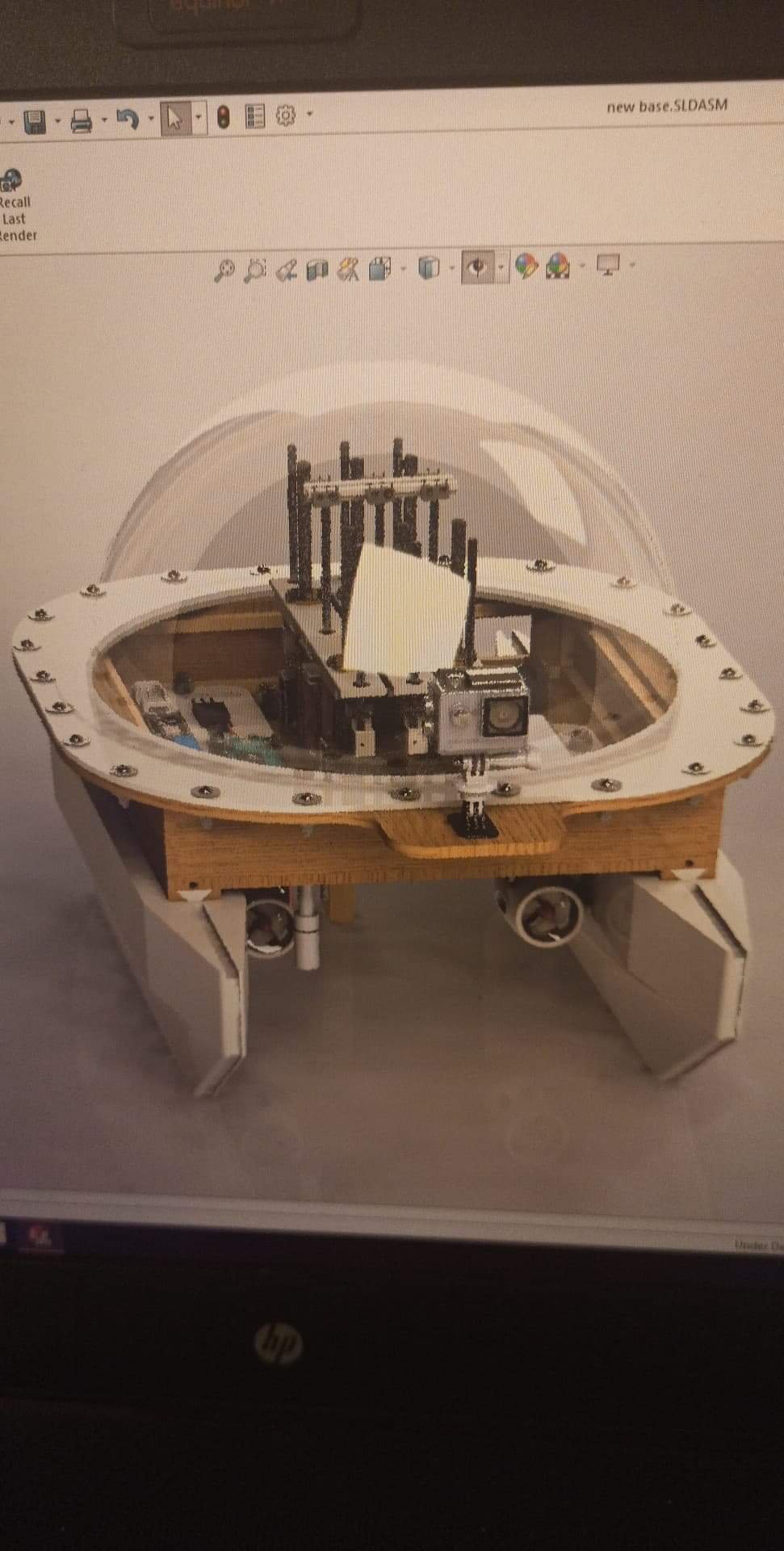
Dental Protection Cover, Prototype Delivered
In the height of the COVID lockdown, a wonderful dentist approached Imperial College asking for help in developing her idea of a COVID-safe device that allows dentists to safely work on patients, with a reduced need of extensive, scarce and expensive PPE.
Working on a prototype during a pandemic was difficult, most of the usual workshops I would be using were closed. I had to outsource most of the metal manufacturing and use what I had at hand most of the time. The most difficult part was finding someone that could vacuum mold transparent plastic, since that was in global short supply because of all the screens people were ordering.
Two prototypes were made, one with rigid moving arms and one with gooseneck arms. There was a steady progression in the quality of the final product. The dentist I was working in ultimately decided to work with a full product development company which undoubtedly was the correct decision for scaling production, doing market research and accessing more robust, consumer friendly manufactured products.
I will not show photos of the ultimate delivered product as that is not solely and exclusively my property.
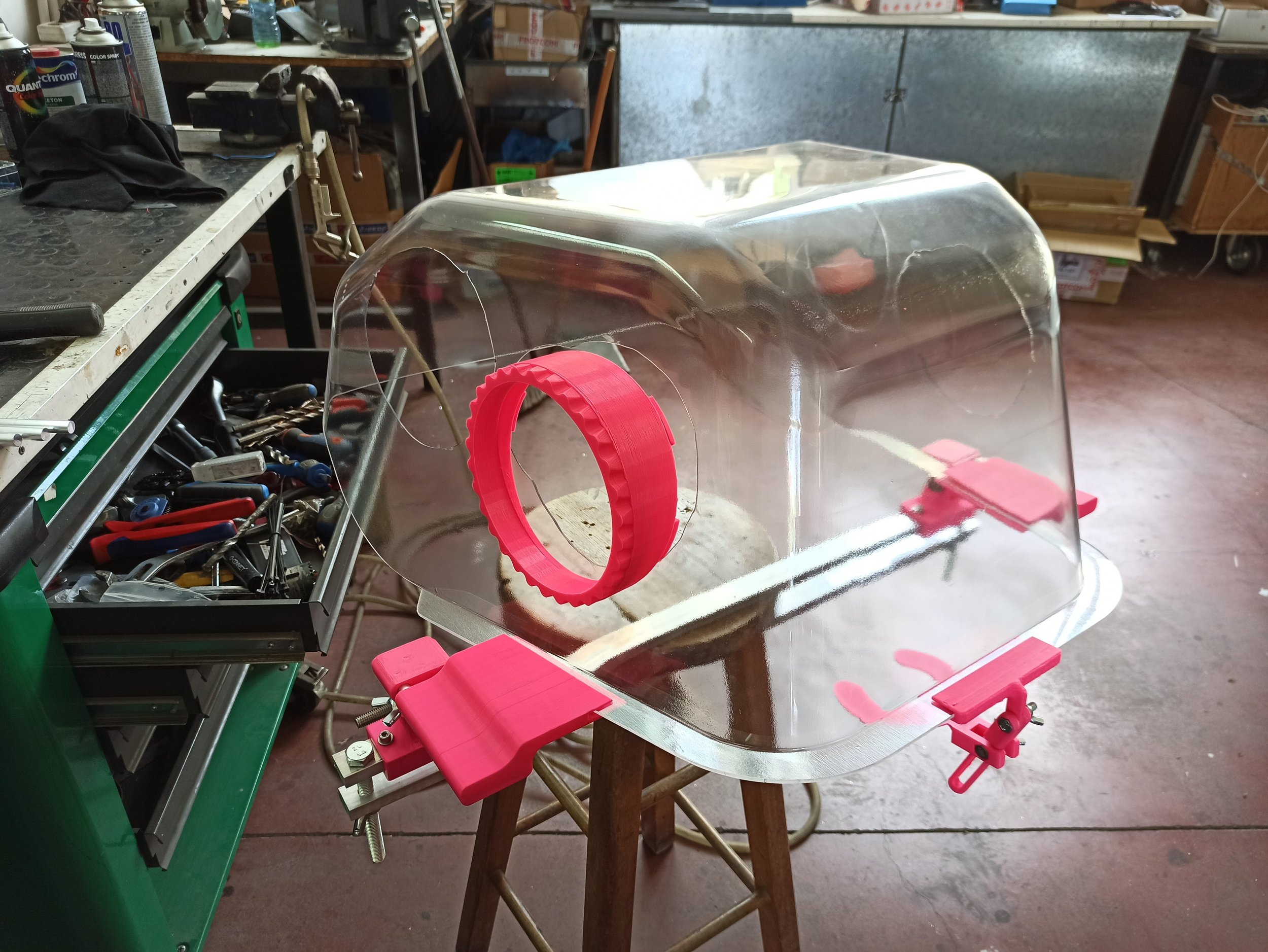
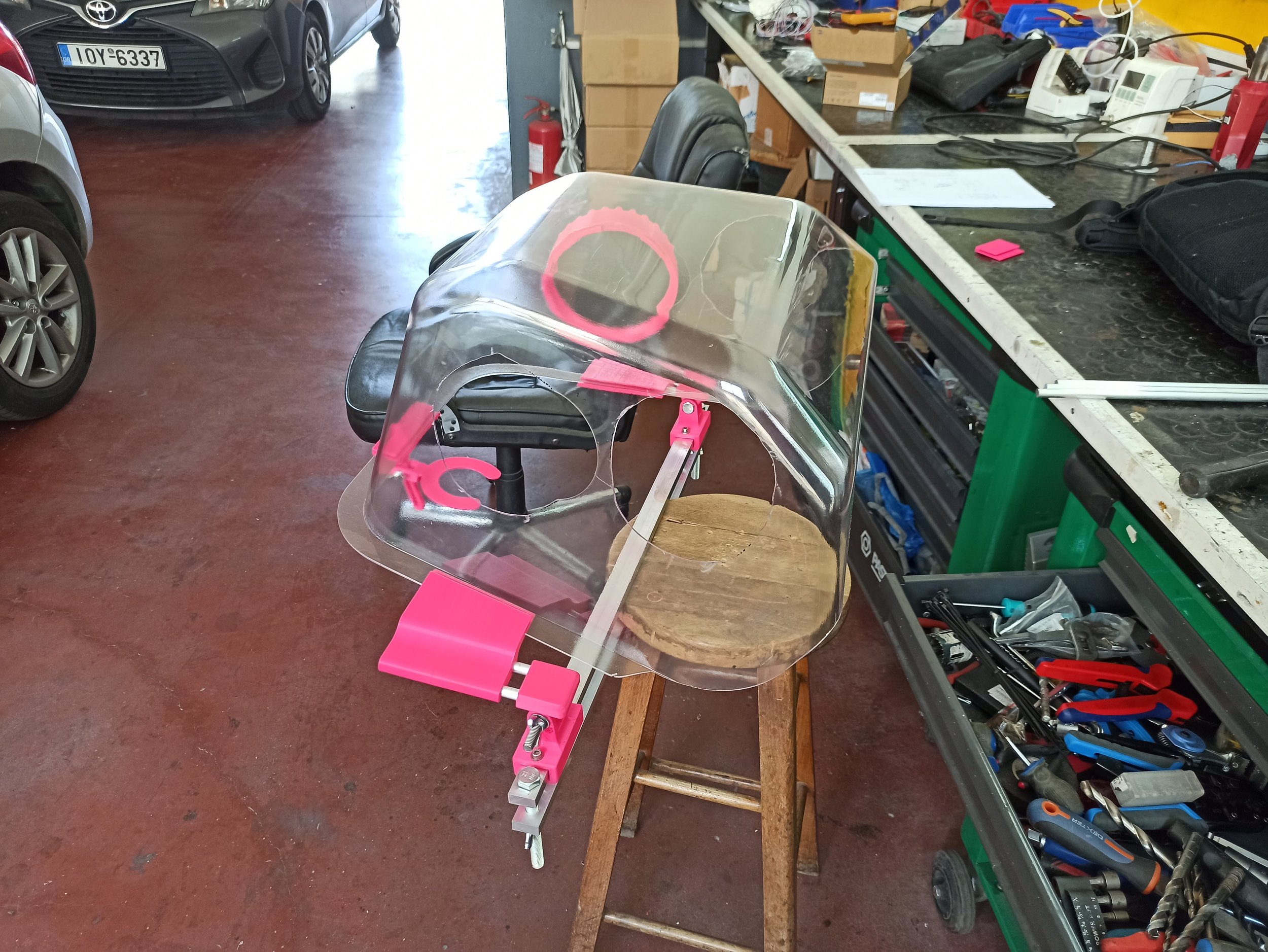
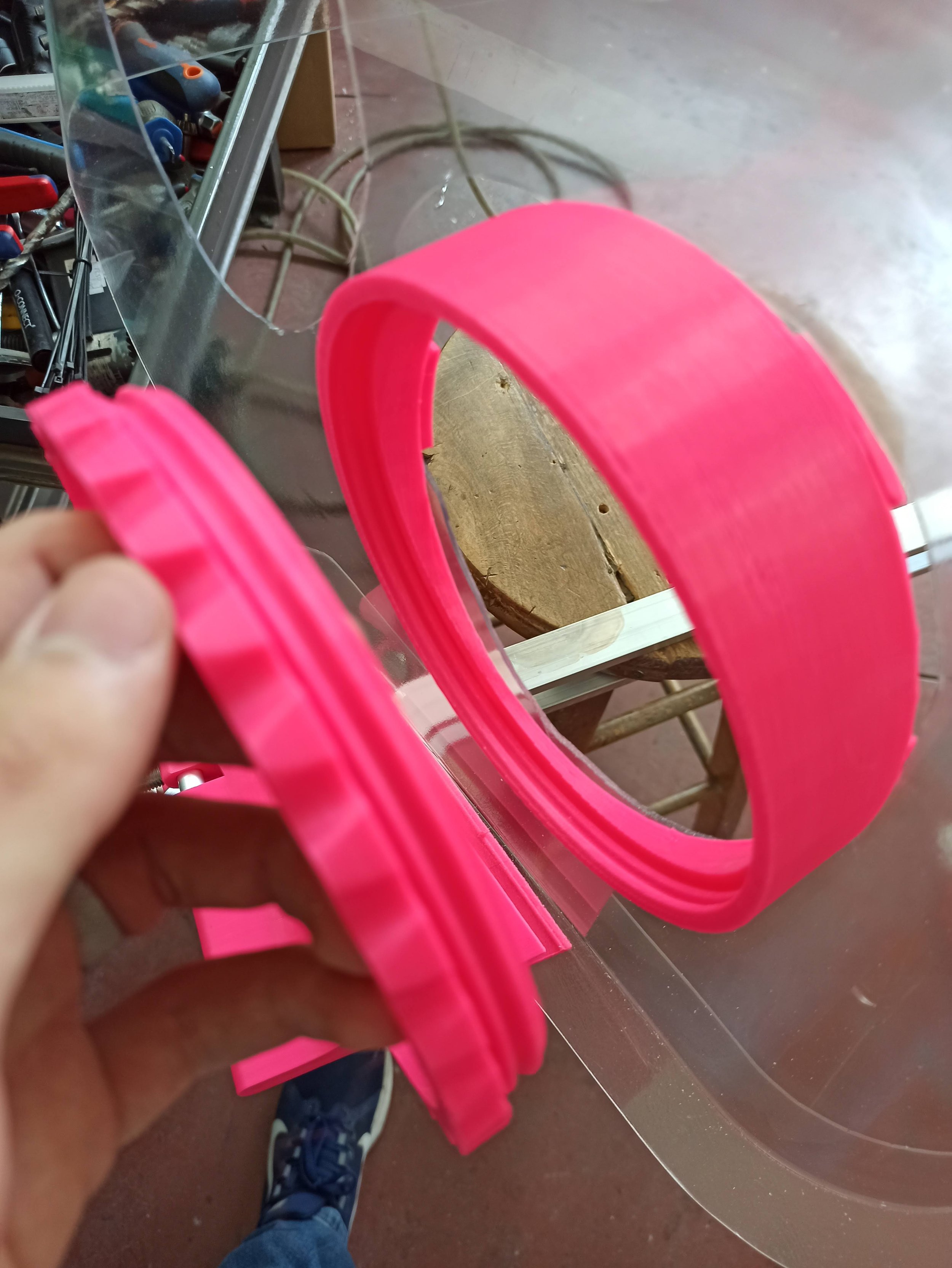
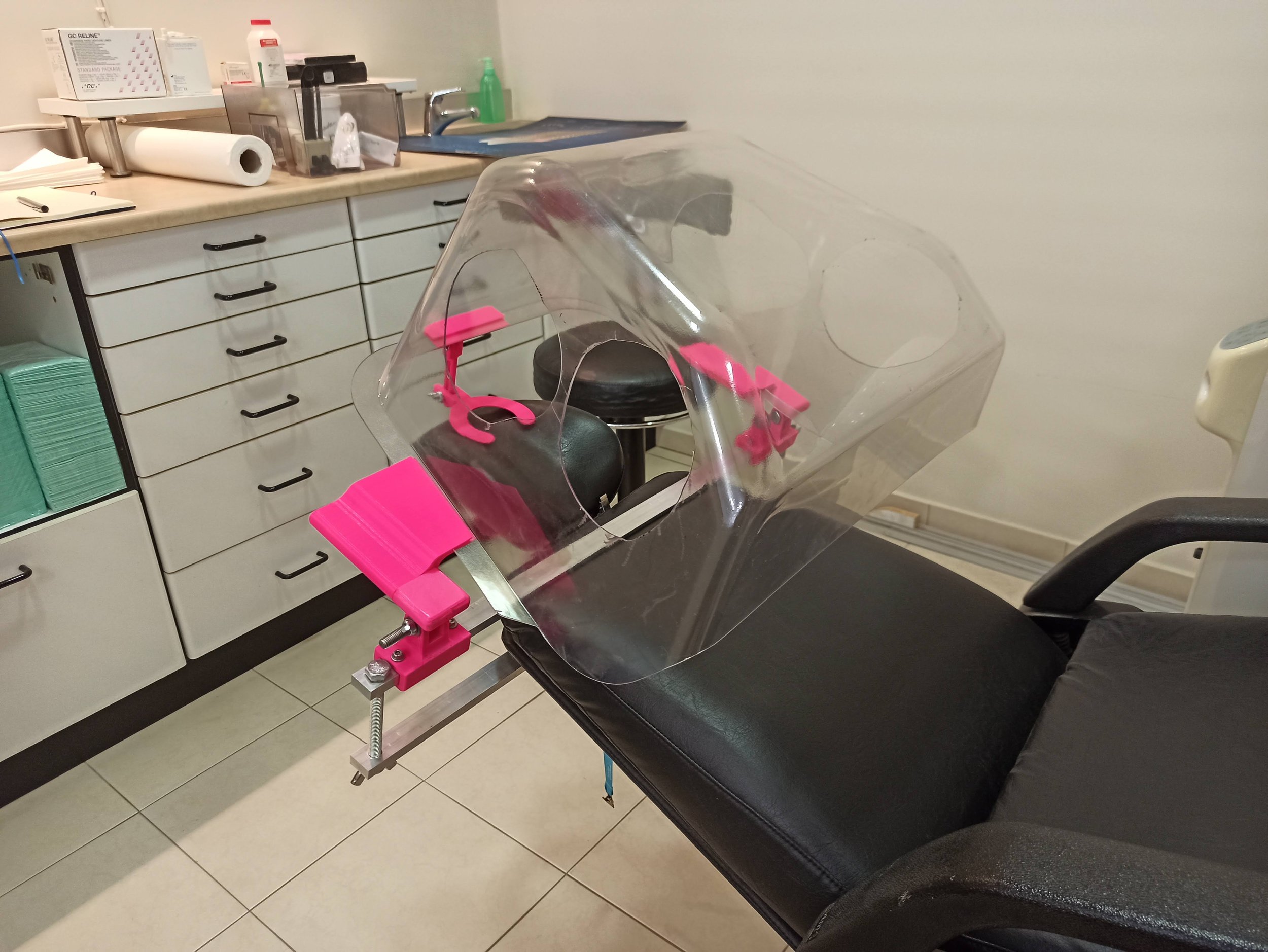
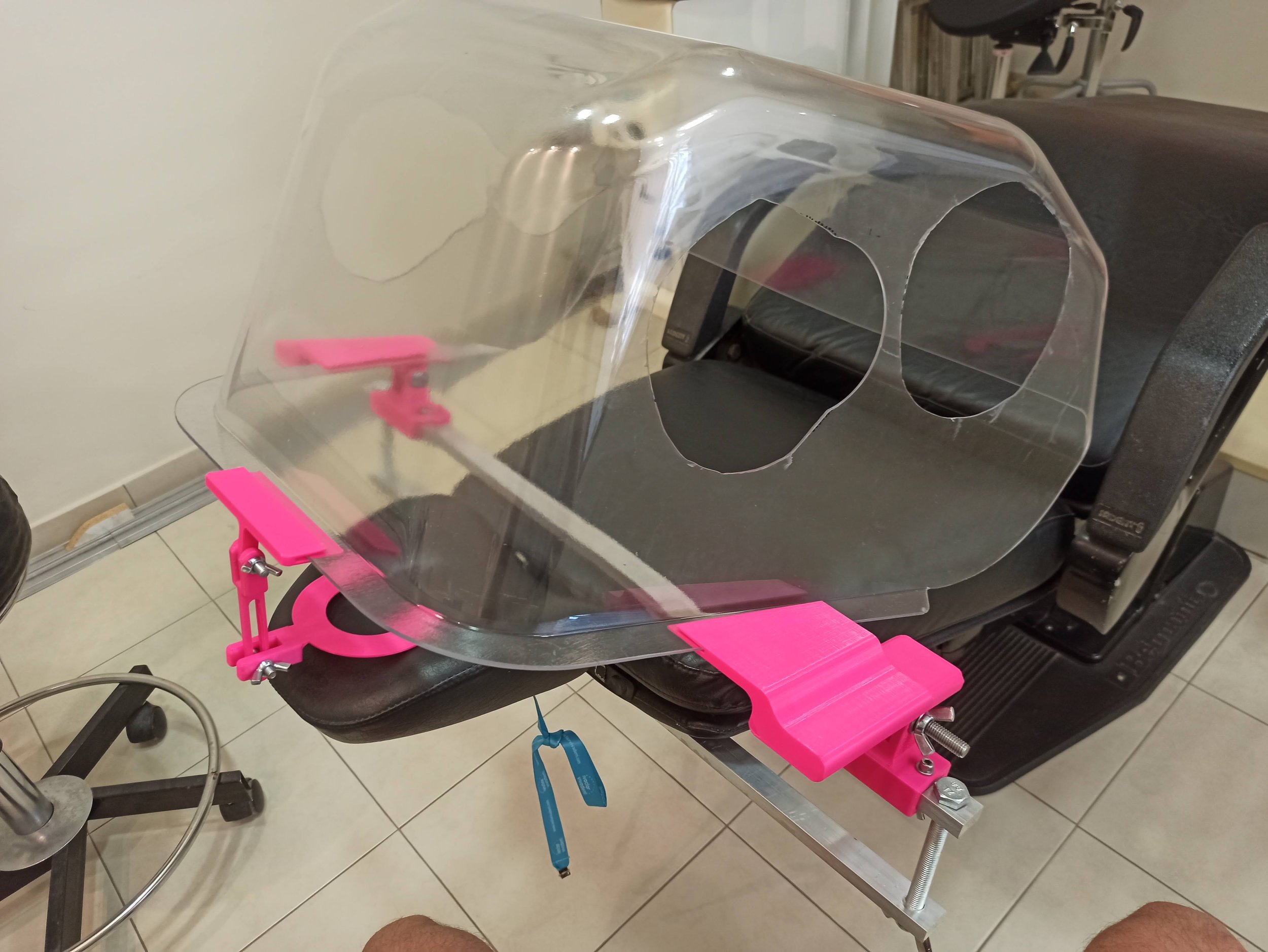
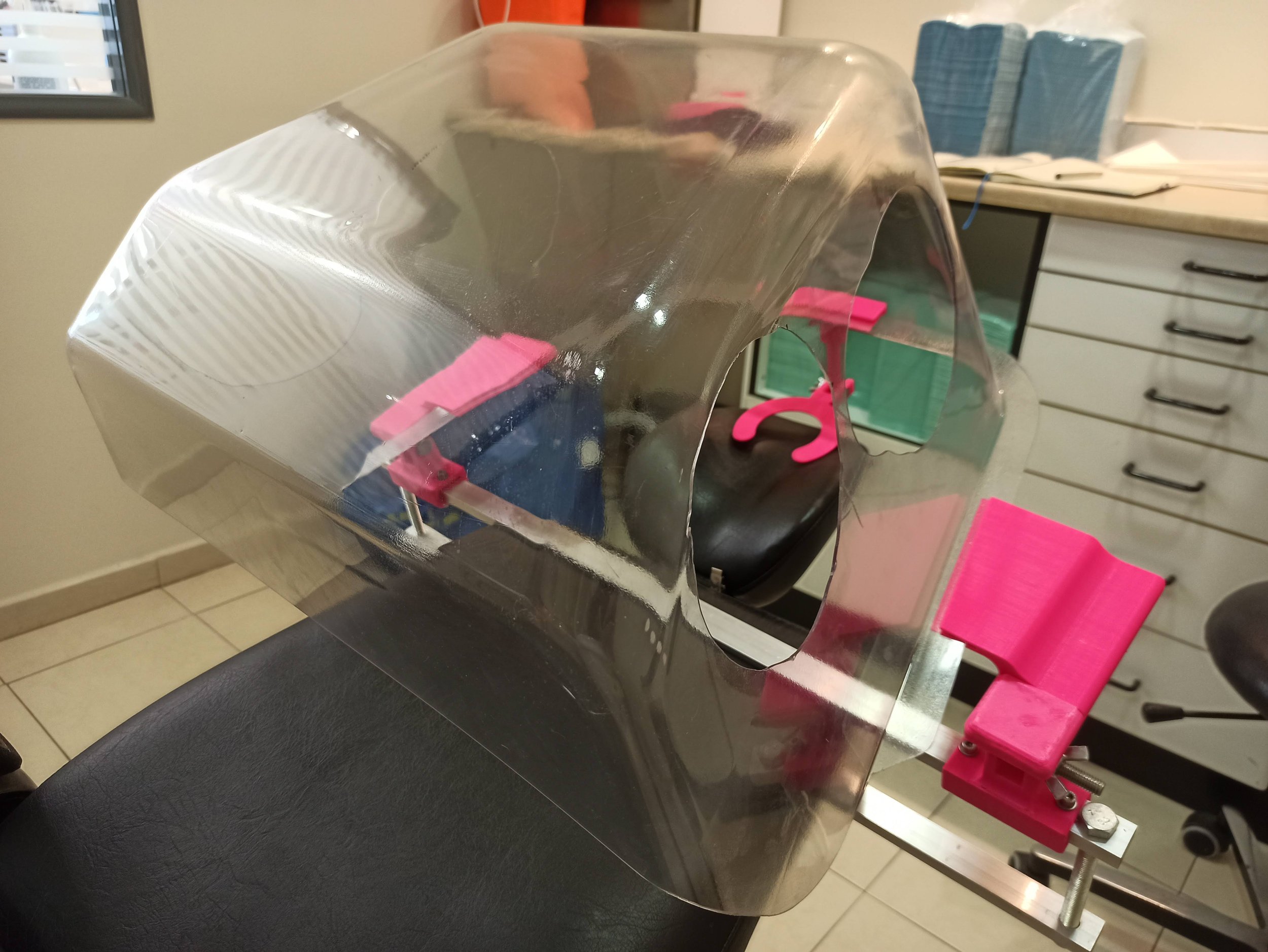
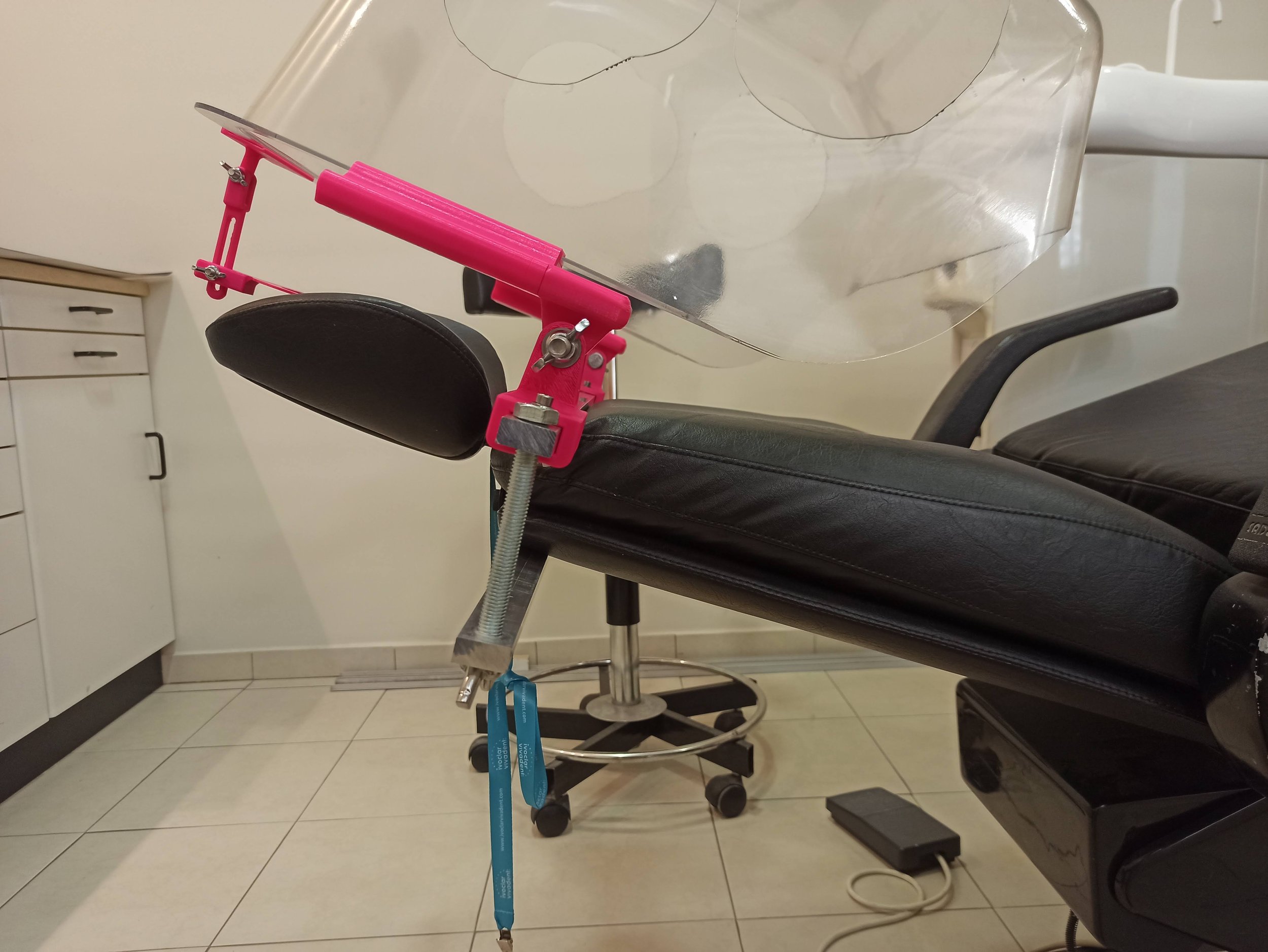
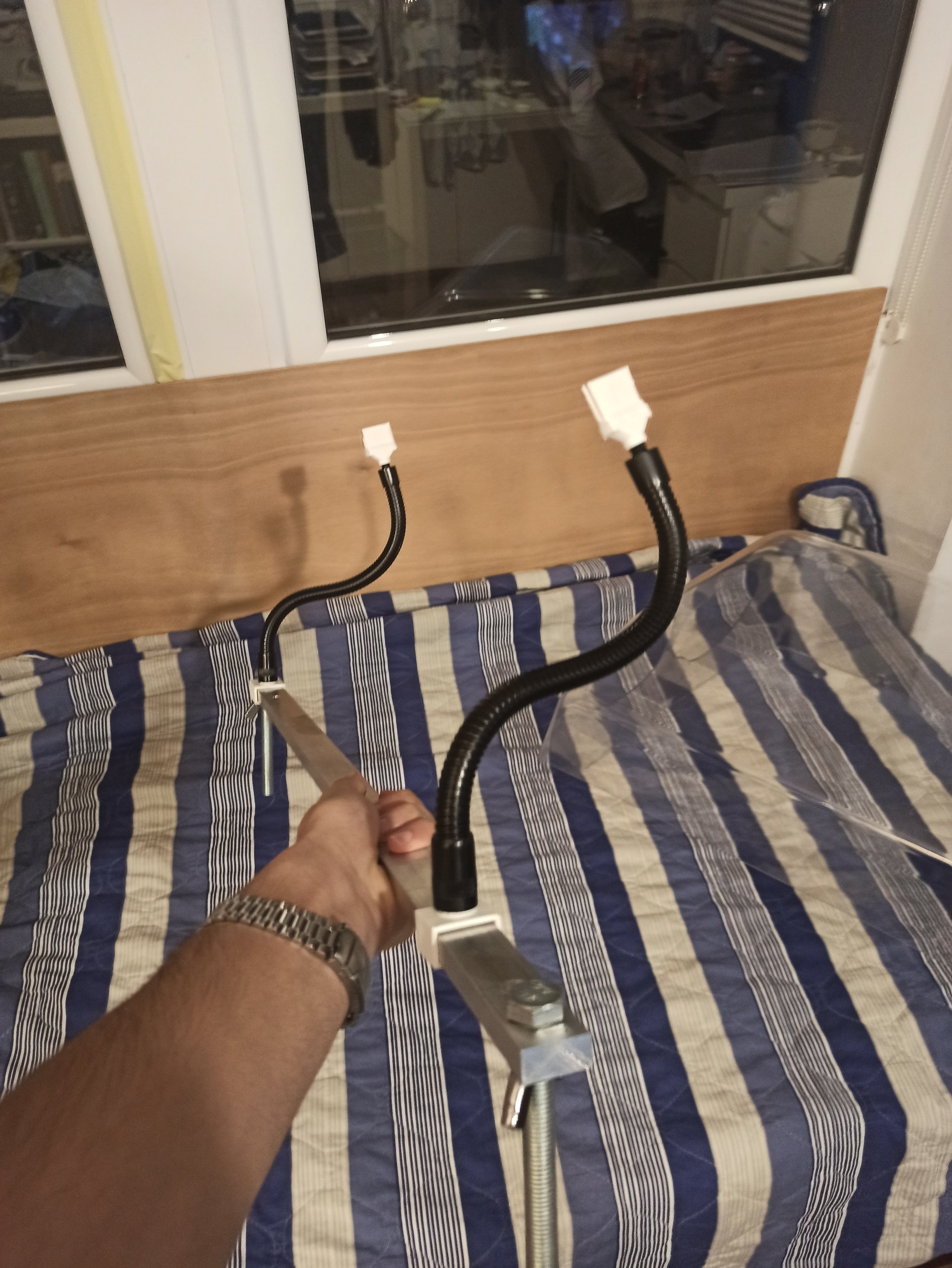
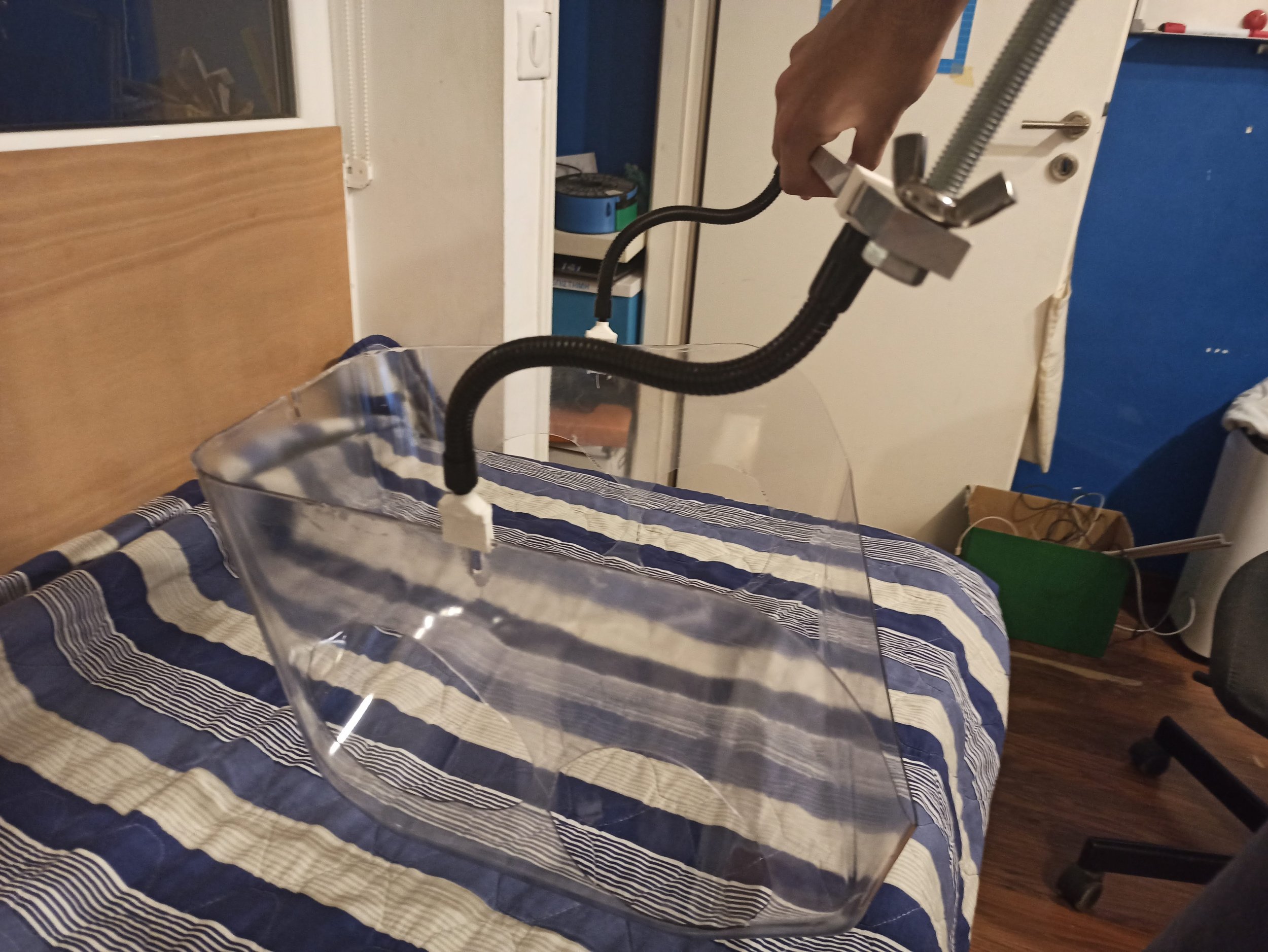
UV Robotics, Product Delivered
During my last year of university I was hired to work on a robotics company, making an automated UV disinfection robot. It was really cool testing it (for short times, outside of the room). The air smells different after we turn the robot on.
I was hired to work as a mechanical and manufacturing engineer, so I worked on the drivetrain module (bottom) and UV module (top). Me and Arnav also worked on all the 3D Printed parts, from making the code for their production to monitoring the printing process.
The robot did get delivered to clients and more copies were made thereafter. It was another time when I remembered and realised that expectations need to be managed and dealines need to be met. As you develop Version1 of something, you have learned so many things and want to improve so many things that you are ready to make Version3. It is really easy to never finish the first version as you constantly improve it, but at some point you need to finish, even if you can make it better. A second chance will come.
Filament Extruder, Still under Construction
It has been a plan of mine, for much time, to create a 3D Printer filament recycler. 3D Printing creates a lot of waste, be it support material, failed prints etc. That wasted material is perfectly good to be reused, where it reformed back into its filament form.
Commercial solutions to this problem exist, but are usually incredibly costly and are targeted to either workshops or high-volume production amateurs. I wanted to create one with a budget of less than 200 pounds. The first prototype was plugged in, and it worked! It of course needs many improvements, but it has at least proven the principle.
As with most things, apparently, COVID also stopped progress on this as well. One of the core parts was a CNC’d lead screw, and when version 2 was in the production queue, the workshop closed. Two years later and the production order is somewhere among many other, newer, more urgent orders.
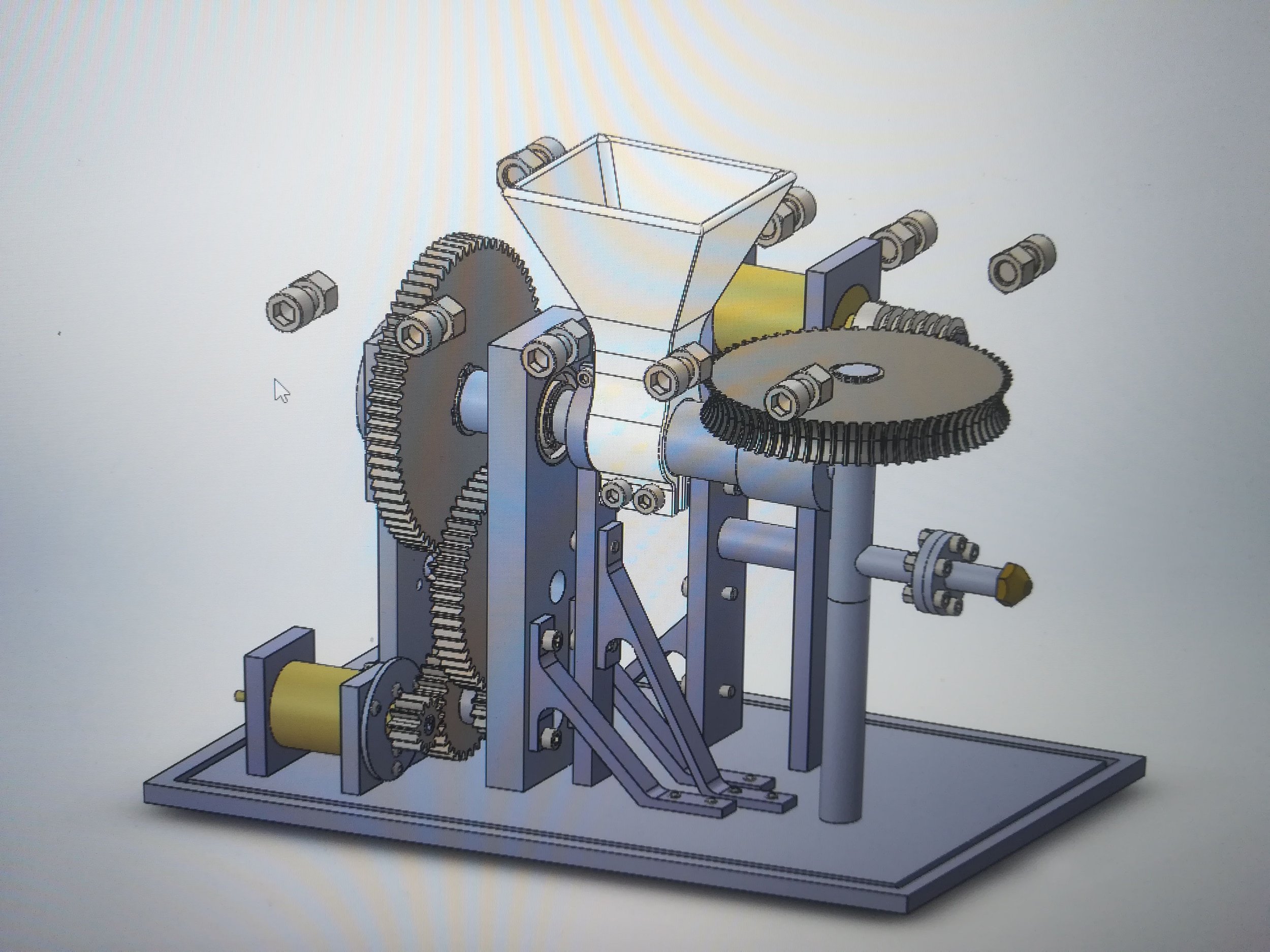
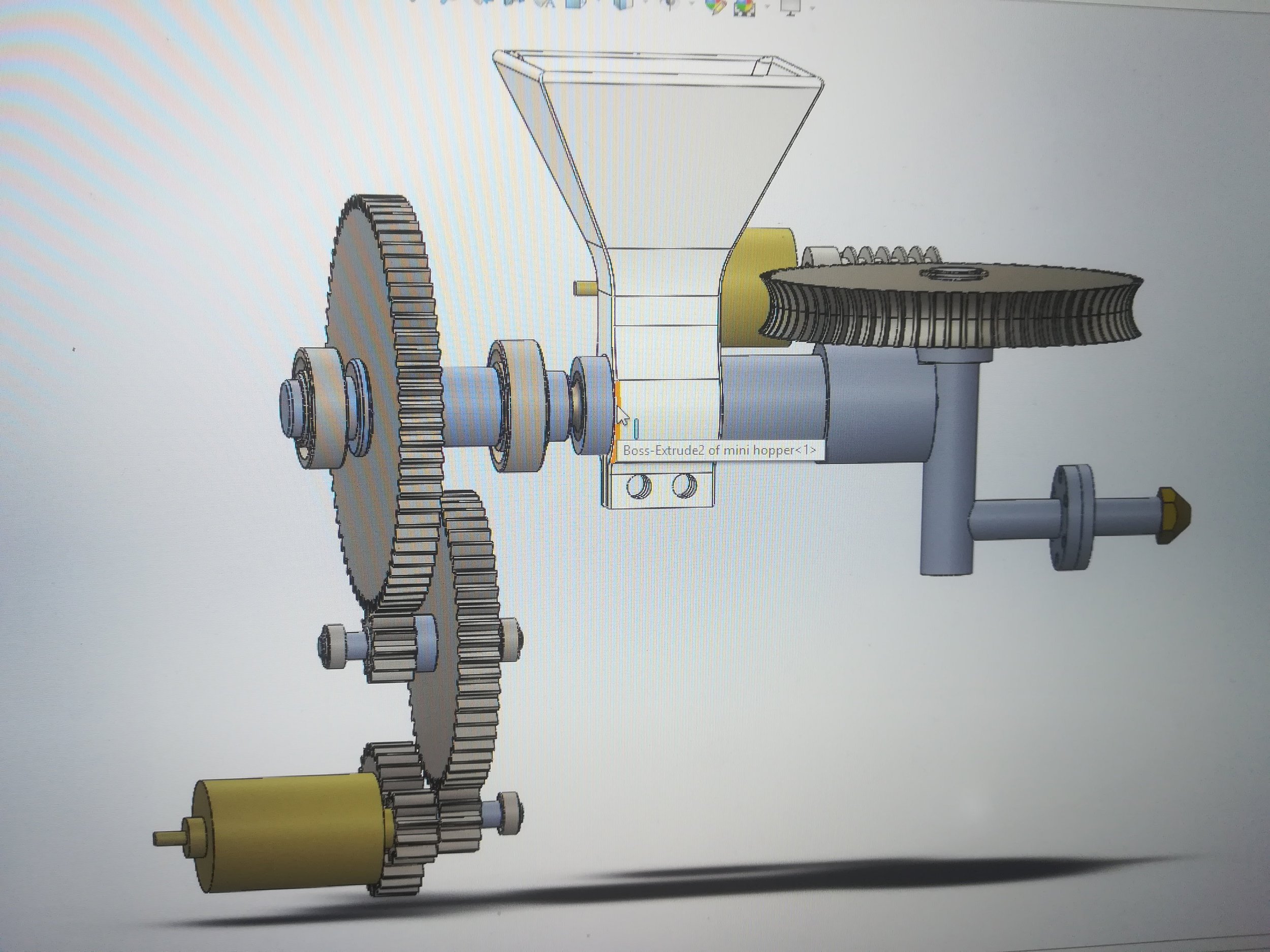
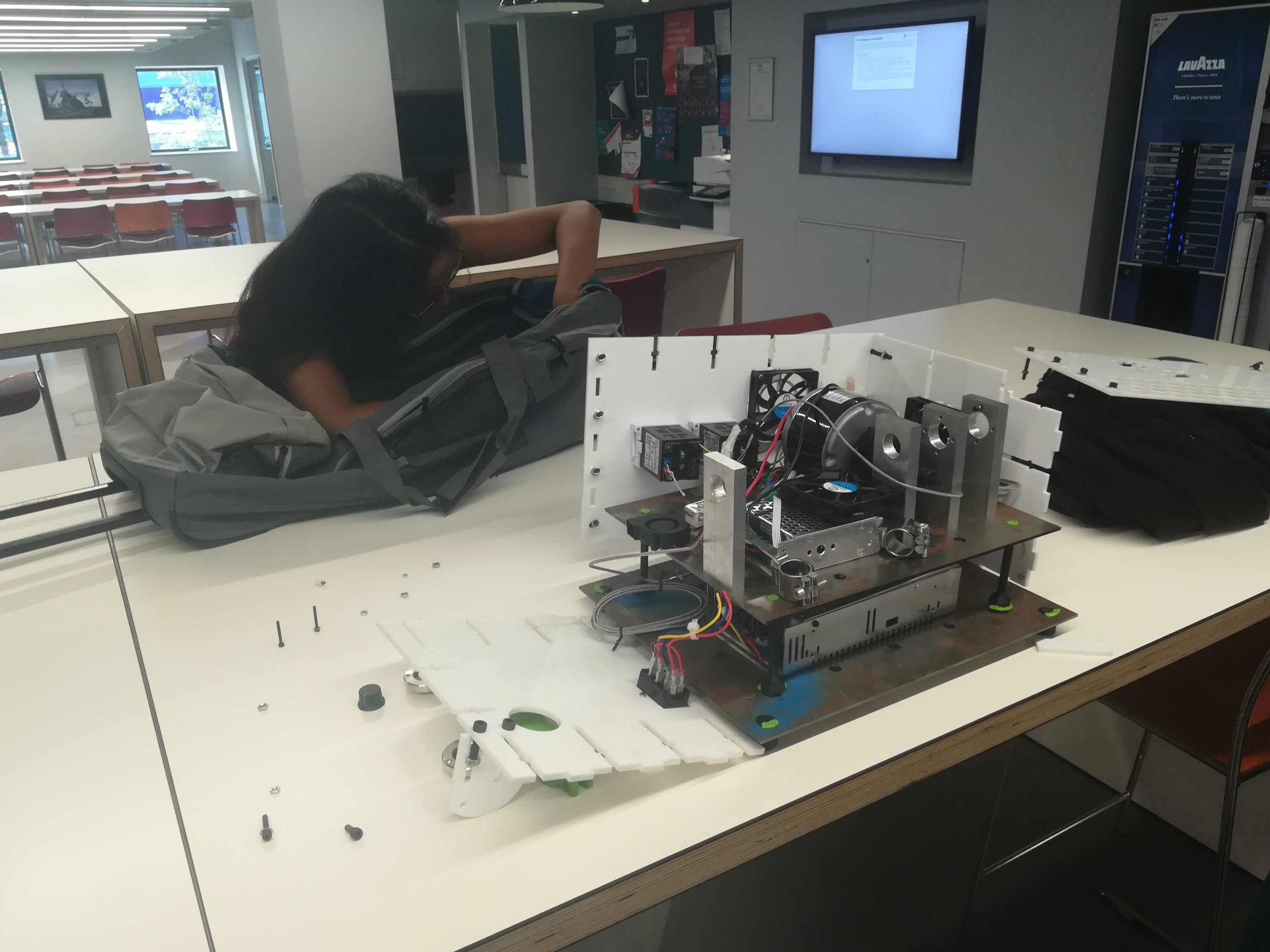
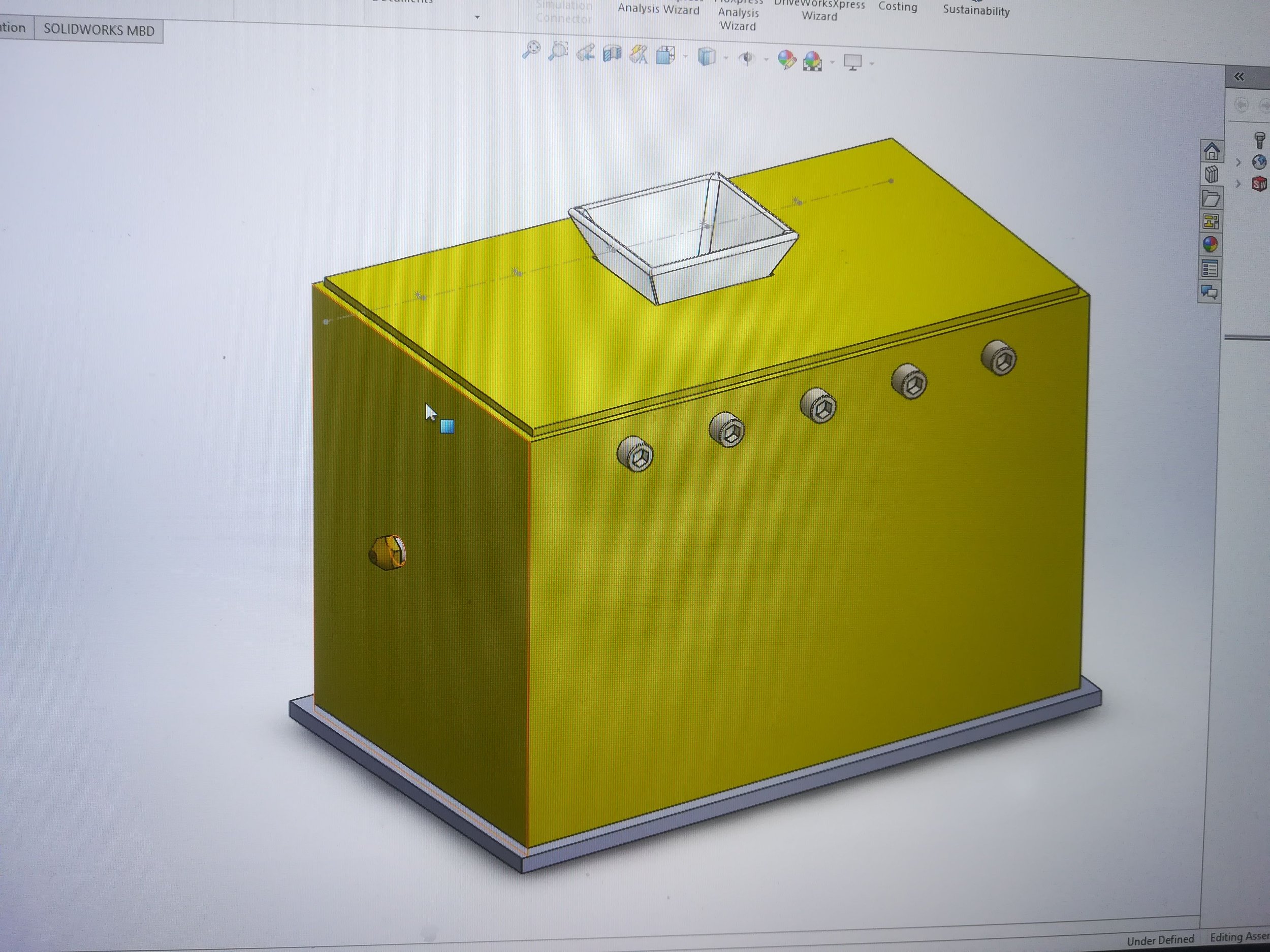
3D Printed Modular Absorption Columns, project on pause
In the beginning of 2nd year me and my flatmate Pierre were bored. We wanted something to work on before the uni workload came down on us. He found a paper from researchers working on a 3D Printable distillation column. We did not like how they used resin to make their device and wanted to try to make one using conventional 3D Printing techniques and materials.
For chemical interaction reasons we could not make a distillation column, but could make a similar absorption column, which pulls CO2 from the air only using running water (for experts, we could not use MEA because it reacts with PLA).
Version 1 is the pink version and it did not work. The coupling between each stage was leaking, the idea to use through-studs meant tightening and assembling the device was incredibly difficult. More critically, we did not create anything new. Version 2 is the one in green, in that we fixed the leaking issue, created one part that worked better than the one used in industry by using the advantages of 3D Printing. We reached 2% absorption without using extra chemicals, which was apparently so good the lab technician was shocked!
Working in “Heavy Industry”
For a year or two I was working remotely for a manufacturing company. They made marine-grade components and were addressed to a broad market. I worked in sales, design, R&D, and general manufacturing whenever I got a chance to work in the factory.
Since I was working in research and development, I worked on many prototypes and parts that may work and be used in production. Below are a set of photos from such time, including the new laser engraving machine I used, a complex tube rolling machine that never went beyond the concept stages, and a time we did some destructive testing to get some maximum load values. Sometimes it is better to use FEA or mathematics with many assumptions, or to just load and break the thing.
I also really liked the blue device I used. It is used to securely grab onto delicate cylinders, while allowing for quick loading and unloading. It was a 3D printed proof of concept that can then easily be remade in metal, made to engage with a single stepper motor. I have it to this day, it is really cool to play with.
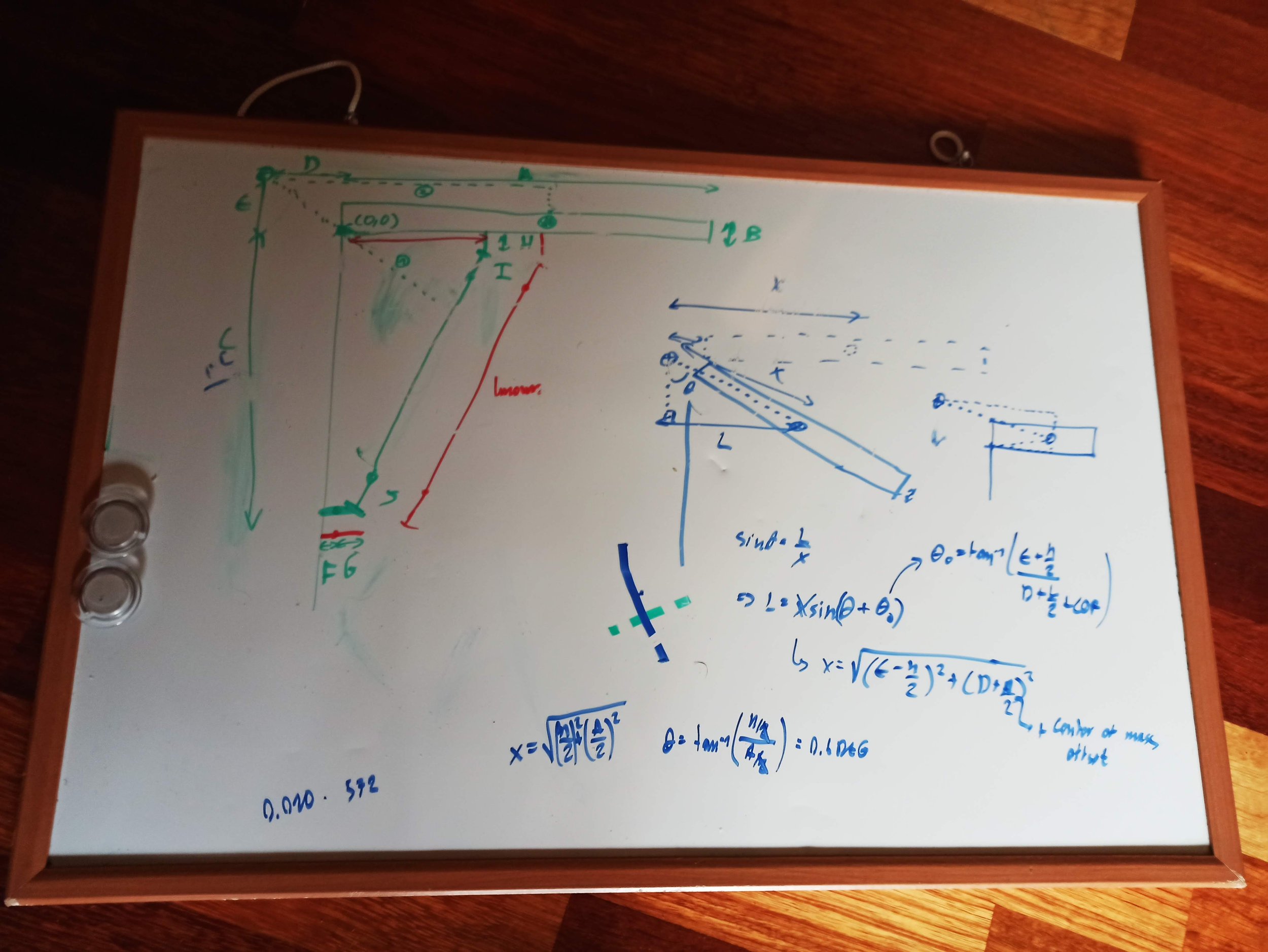
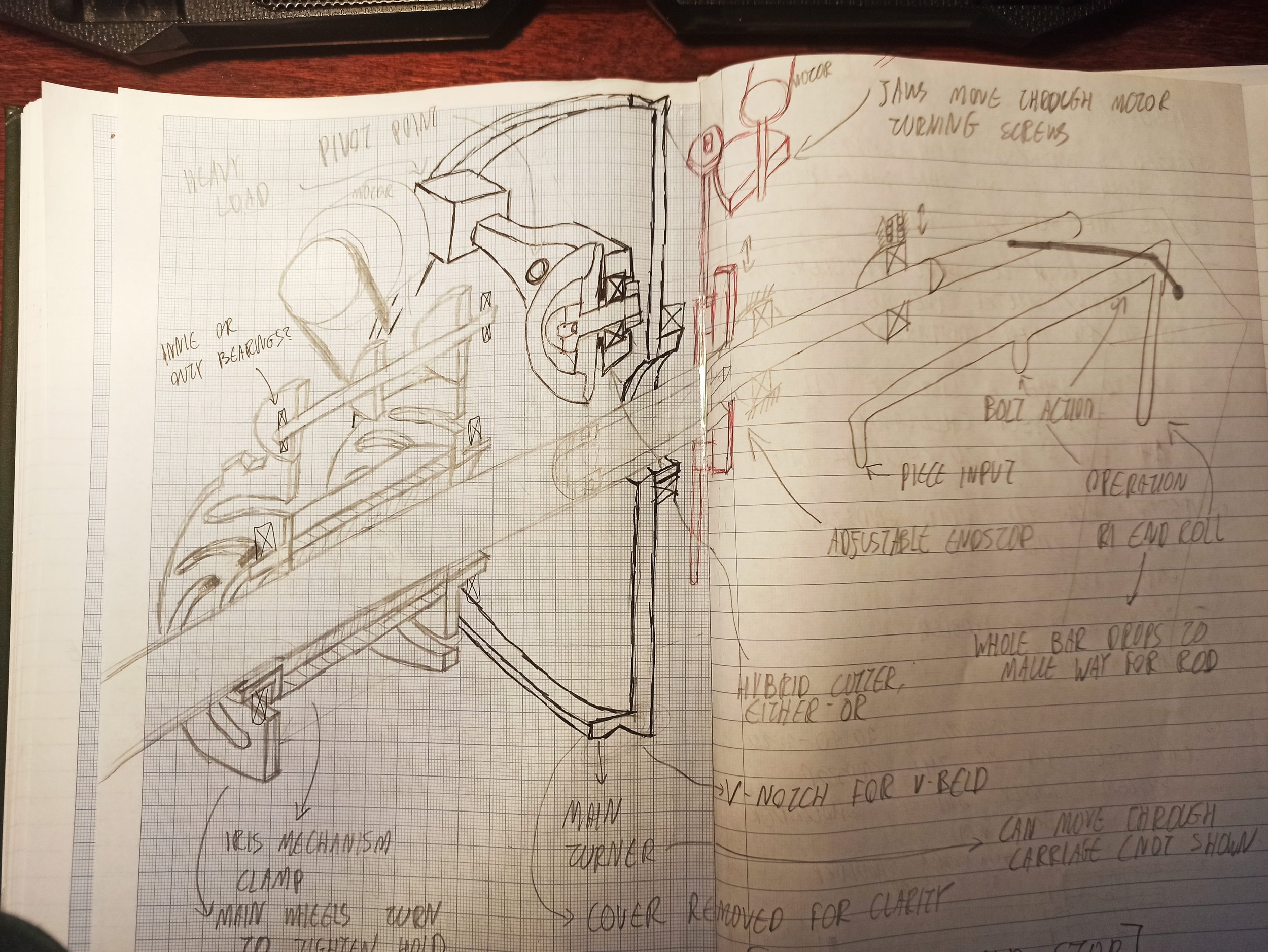
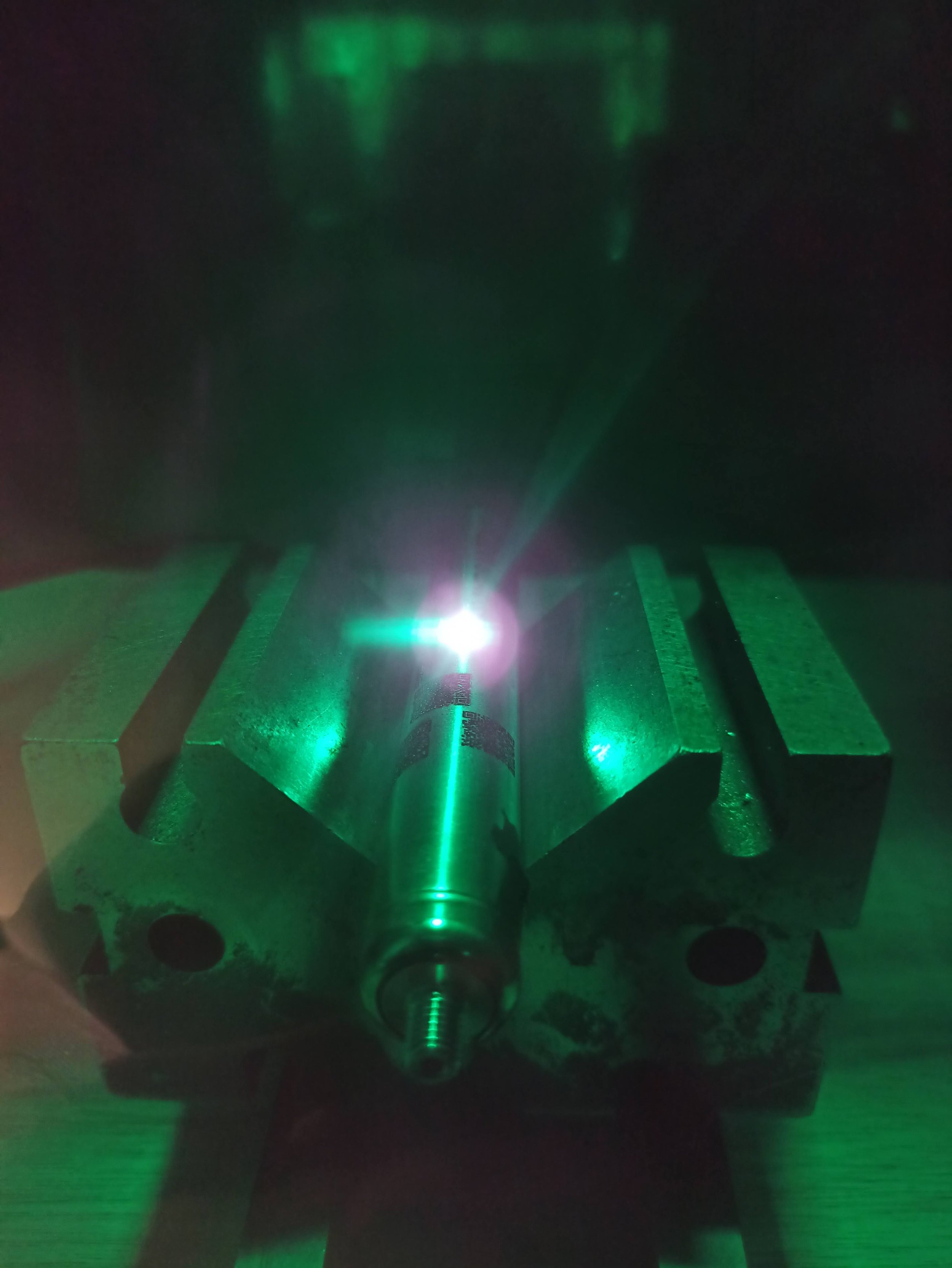
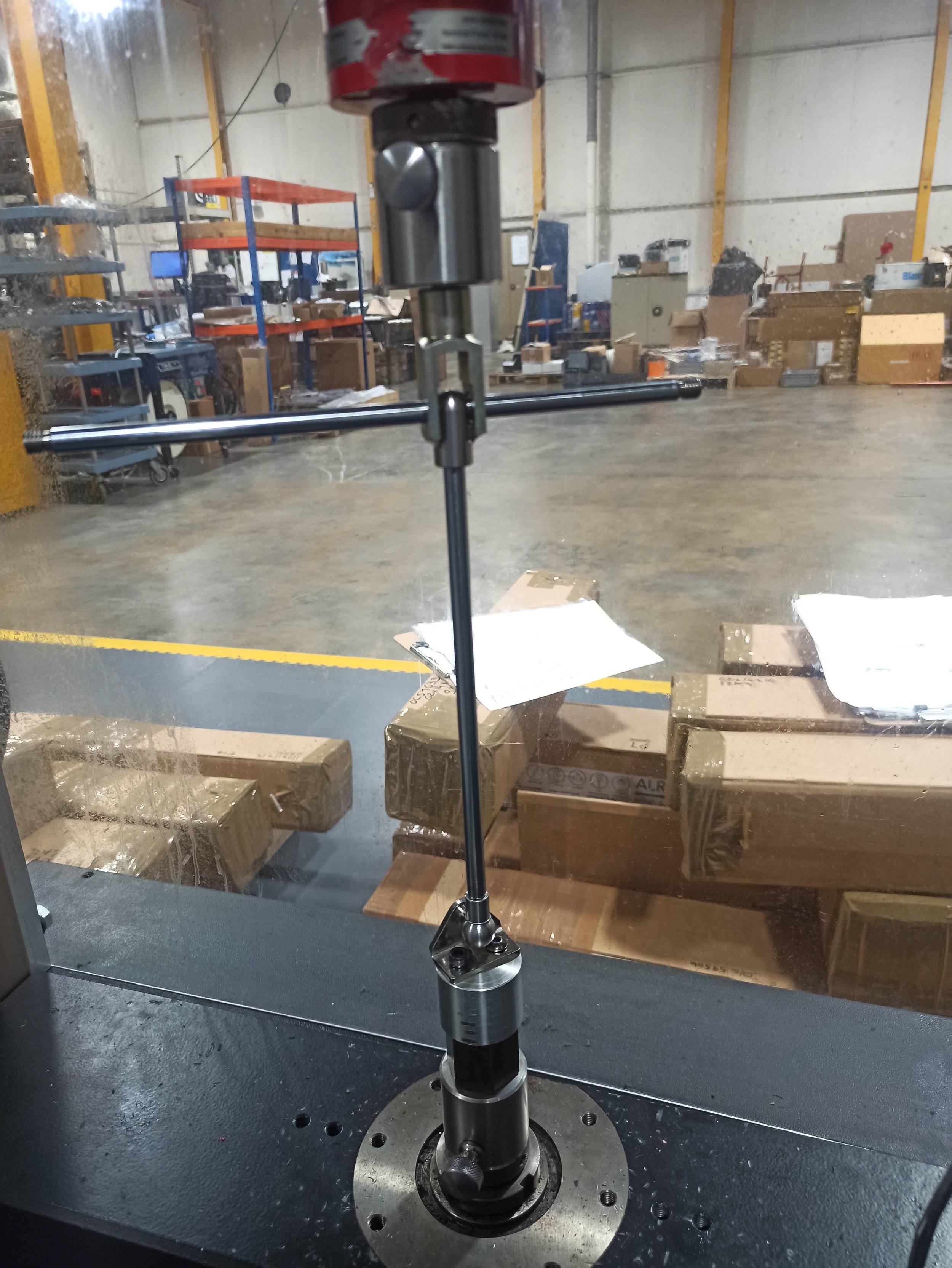
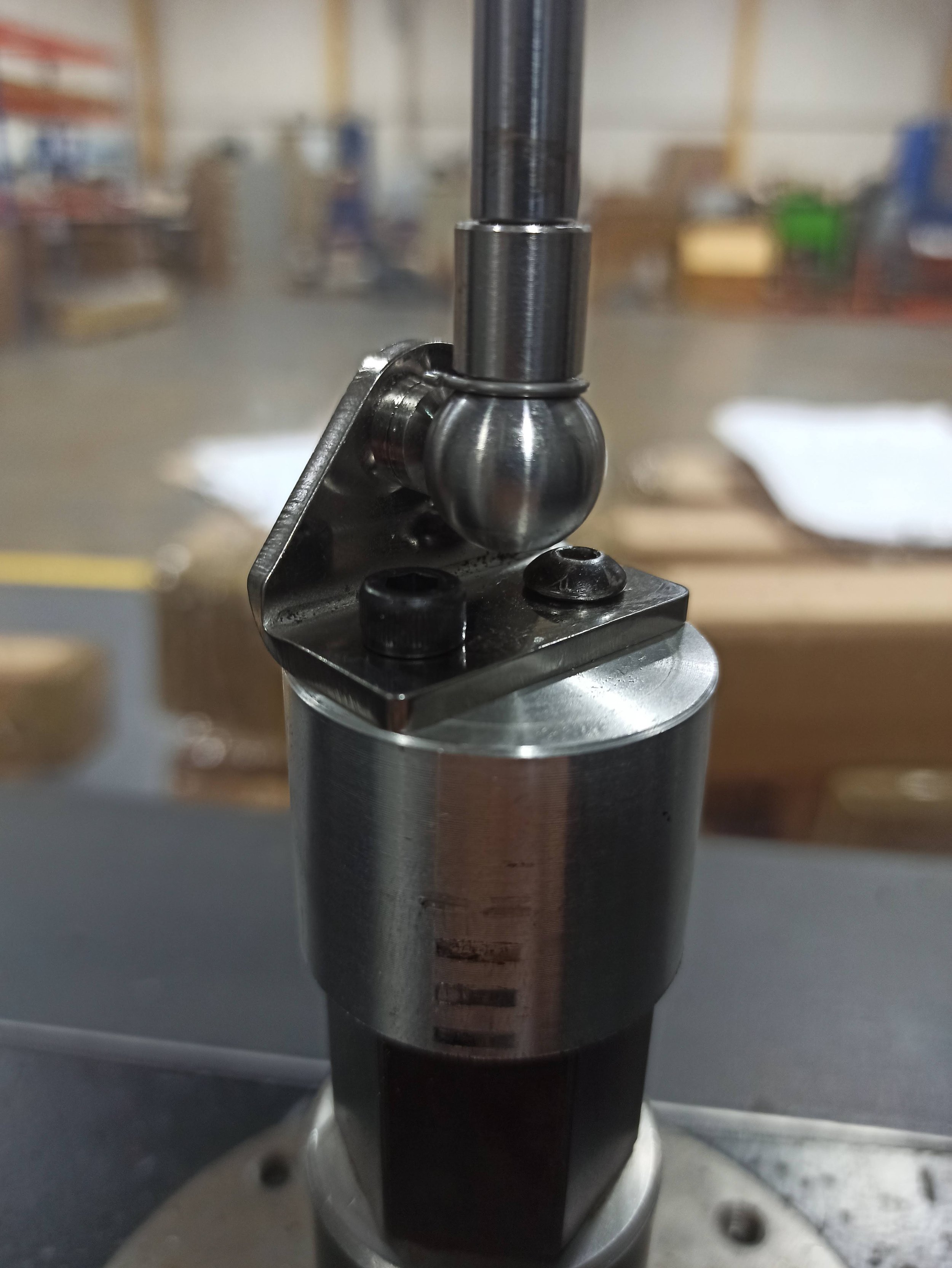
Artemis: Project Delivered
In the 3rd year of my degree I took up the Embedded C for Microcontrollers module, or ECM. In ECM the goal is to make a small robot-rover which tracks an IR beacon, reaches it and reads a nearby RFID tag, and returns to the point it started. All functions of the robot, from controlling the motors, to the pathfinding, to RFID reading and check-summing was written on a PIC microcontroller by me and my teammate. During testing our robots and algorithm proved to be among the fastest and most efficient in the group. Notice the cardboard bodge in the front of Artemis, this was because the IR sensors on the front were not working as intended, as they were not accurate enough to separate the left and right signals.
Various projects I cannot find enough photos for.
I am not used to taking photos of projects I am working on, most of the content I do have is for updating teammates, making presentations etc. I have some projects which are not thoroughly represented, so I will include them in this section here.
The first bit is from the 4th year Manufacturing Technology and Management course, part of which was learning how to code CNC parts for machining. We had to design the part in grey from a generic stock block. This video shows the operations I coded once the block was brought to size. This design was of course accompanies by custom tooling, custom workholding etc.
The second bit is from the Design Week project during my 2nd year of studies. The context is that we (team of random 4 people) were tasked with designing a device that can charge a phone through river water power. “Design” starts with concept design and ends with a prototype-ready model. I worked on the bulk of the digital design, while my partners focused on calculations, manufacturing scaling, and other issues.